2024 CFSEI DESIGN EXCELLENCE AWARD WINNERS
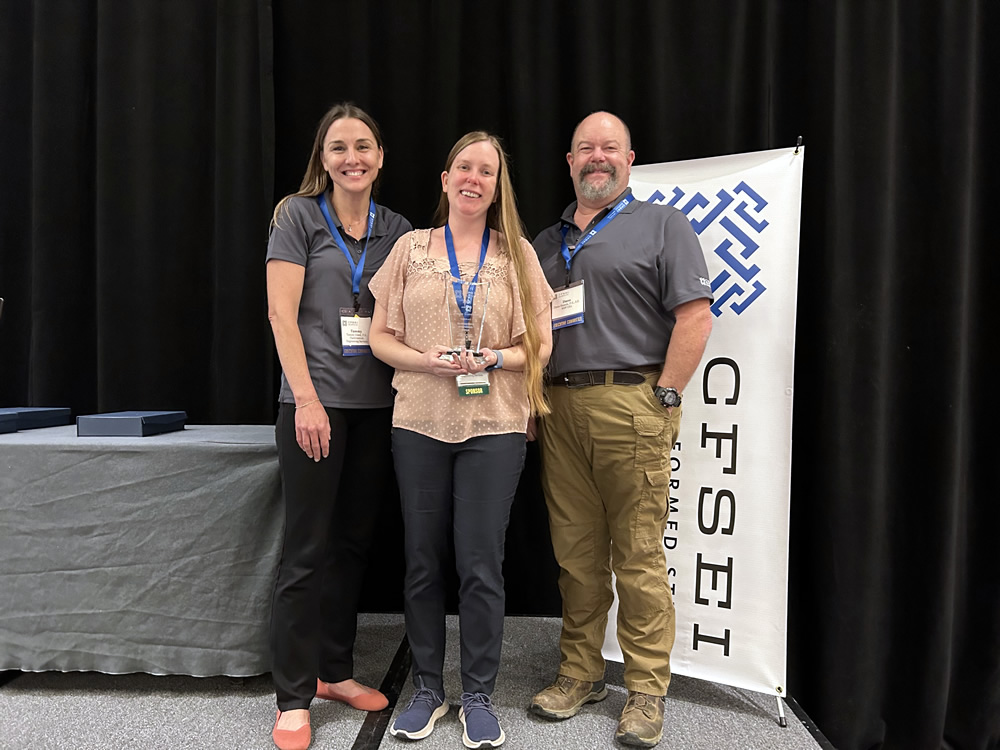
THIRD PLACE
CLARKDIETRICH ENGINEERING DESIGN – IQHQ RESEARCH AND DEVELOPMENT DISTRICT– BLOCK 2A SAN DIEGO, CALIFORNIA
IQHQ Research and Development District – Block 2A 525 N Harbor Drive San Diego, CA 92132
Completion Date: October 2023 (Framing Complete) Construction Cost: $50 Million
Owner: IQHQ Architect of Record: Erin Lilly, Gensler. Engineer of Record for Structural Work: Eric Lehmkuhl, KPFF. Cold-Formed Steel Specialty Engineer: Jennifer Sexton, ClarkDietrich Engineering Design; Brett Olson, P.E., ClarkDietrich Engineering Design; Tammy Gleed, P.E., ClarkDietrich Engineering Design. Cold-Formed Steel Specialty Contractor: Tim Almond, Brady West. Award Entry Submitted by: Jennifer Sexton, ClarkDietrich Engineering Design.
Project Background
“The Research and Development District (RaDD) is downtown San Diego’s newest life science mixed-use development,” the Gensler website says. “Sitting on eight acres and occupying six city blocks, San Diego’s Research and Development District will represent the largest urban commercial waterfront site along California’s Pacific coast, once complete. Designed by Gensler, this dynamic urban life science campus will feature a mix of mid-rise buildings, a 17-story tower, ground-floor retail, restaurants, and a public paseo, all activated by roof decks and green space for the community to enjoy.”
IQHQ – Block 2A is one of the six-buildings that make up the Research and Development District in downtown San Diego.
Design Challenges and Solutions
The picture frame feature on the north elevation was a primary design challenge on this project. The cladding cantilevers up to 5’-6” beyond the primary structure on all four sides of the curtainwall window. Supporting the gravity load of the side walls of the picture frame required kickers every 6’-0” o.c. vertically.
Another difficulty involved several continuous louvers at the first floor. Through coordination with the design team a solution was reached where a louver would be place in 8’-0” increments to allow for jamb framing in between.
Throughout the project, there were several locations where the wall width varied along its height, or where bypass studs were partially interrupted by floor slabs. The design used lapped studs and unique spandrel framing to achieve the shape desired by the design team.
At a location with high loads a creative detail was needed for reinforcing the deflection track. Two studs were added, one on each side of the deflection track, to help strengthen the track legs.
Click here to view the drawings
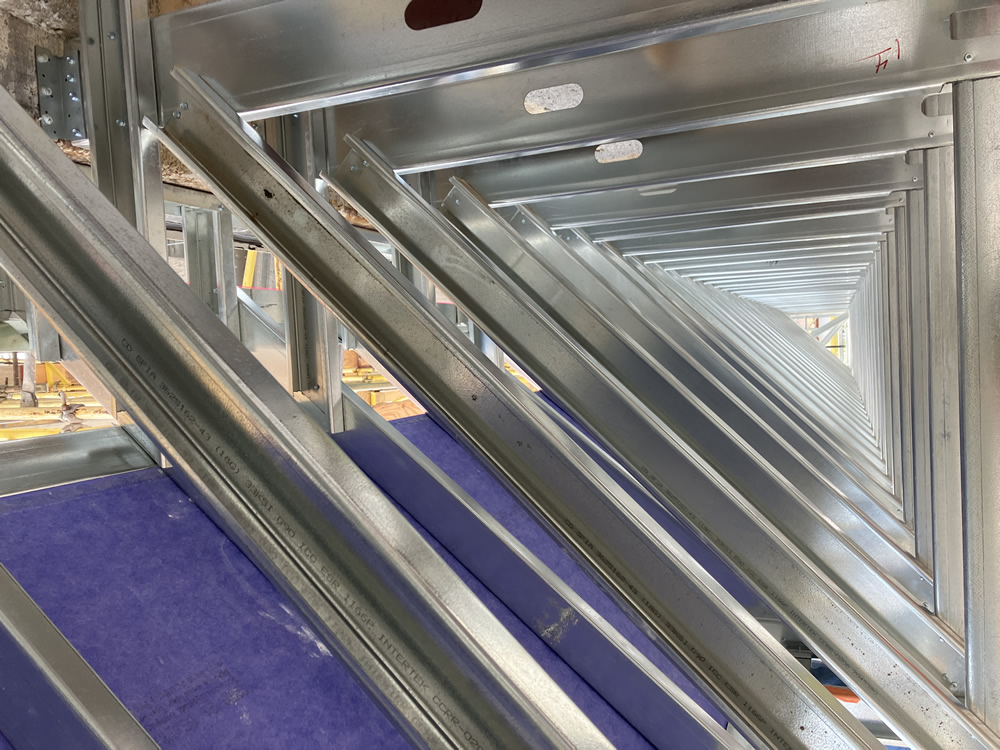
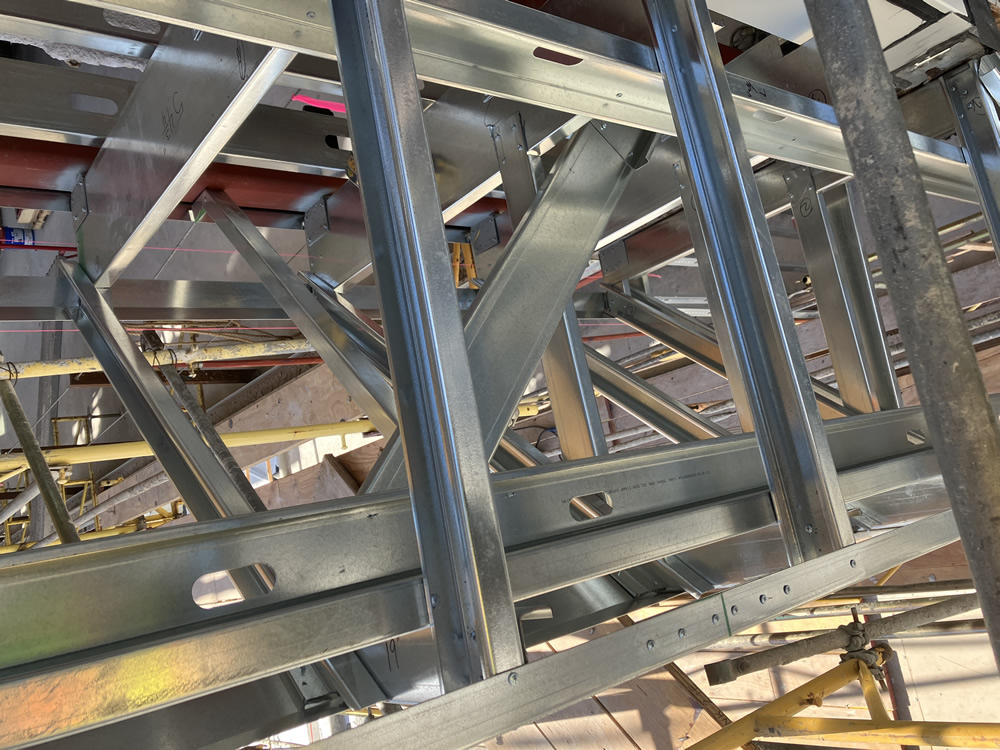
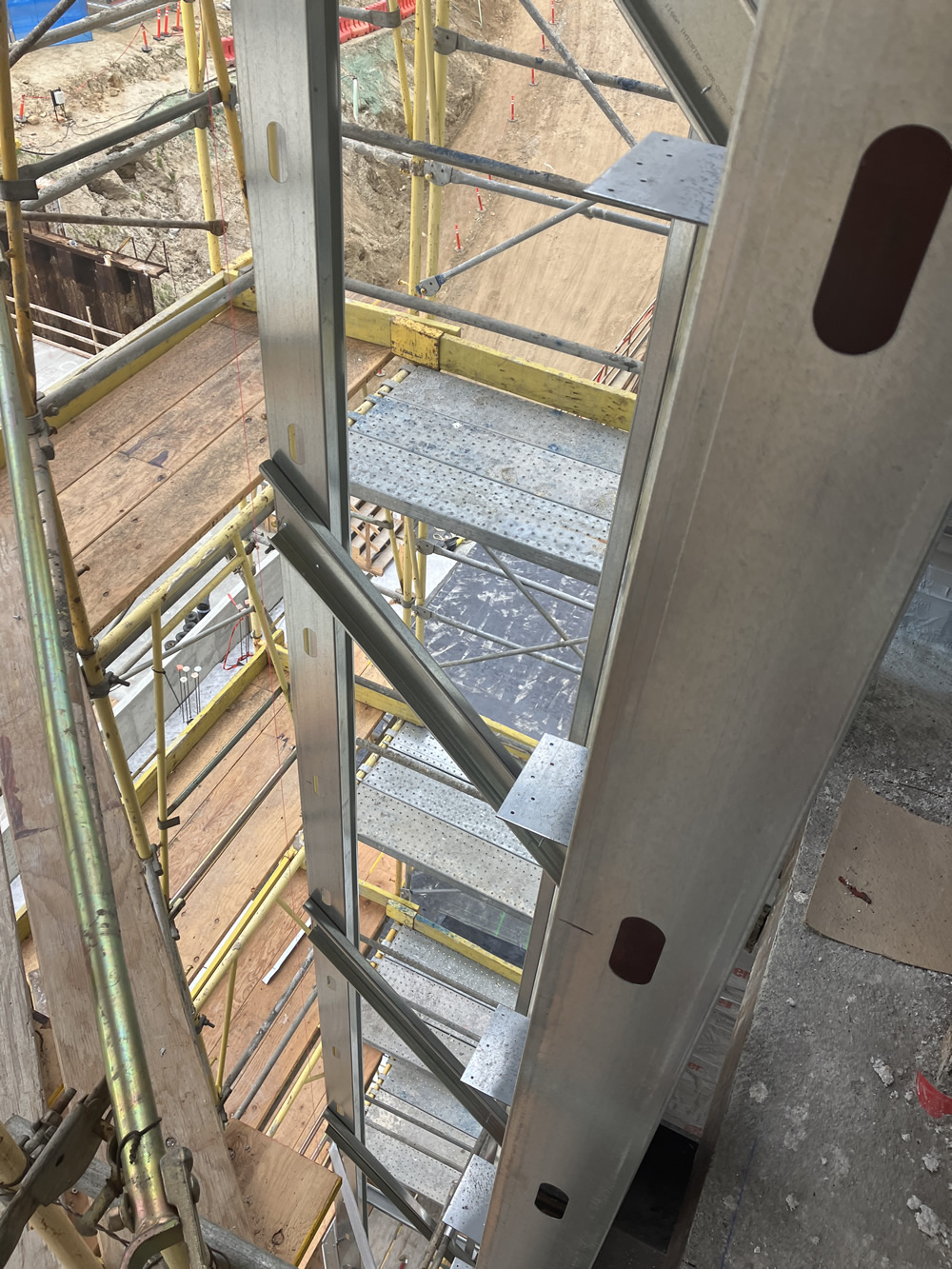
|