2022 CFSEI DESIGN EXCELLENCE AWARD WINNERS
SECOND PLACE – MUNICIPAL/SPORTS
EXCEL ENGINEERING – COLUMBUS CREW STADIUM COLUMBUS, OHIO
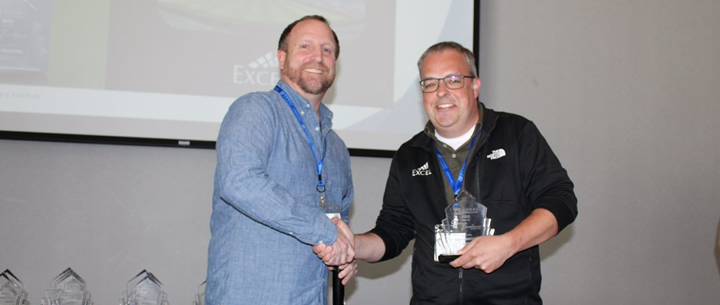
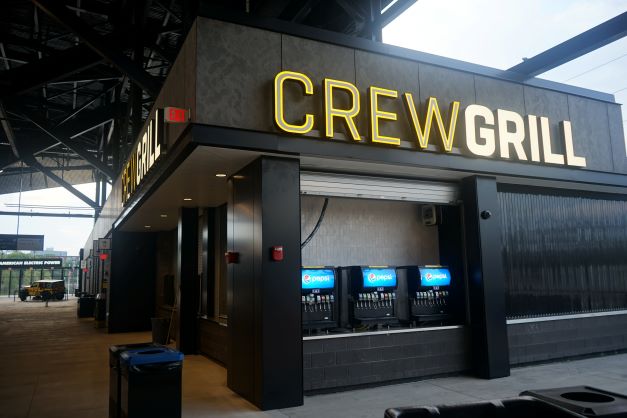
Columbus Crew Stadium 96 Columbus Crew Way Columbus, Ohio 43215 Completed: July 3, 2021 Construction Cost: $314 million
Owner: Crew SC Stadium Company, LLC Architect of Record: Christopher M. Migneron, HNTB Engineer of Record for Structural Work: Michael W. Shelton, HNTB Cold-Formed Steel Specialty Engineer: Andrew Seibel, Excel Engineering Cold-Formed Steel Specialty Contractor: Kris Edwards, Valley Interior Systems Award Entry Submitted by: Andrew Seibel, Excel Engineering
Project Background
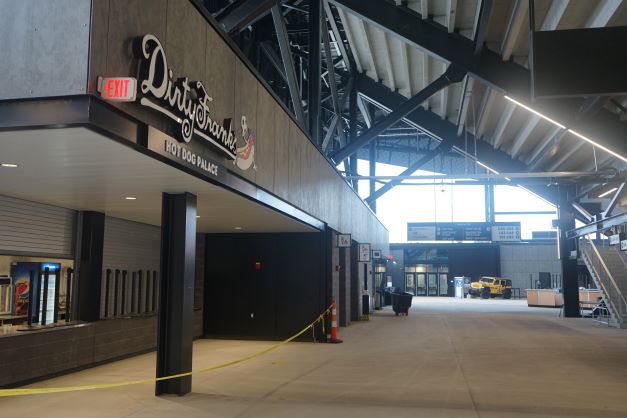
Breaking ground on October 10, 2019, the Lower.com Field soccer stadium began construction to replace the aging Mepfre Stadium in Columbus, Ohio. With a construction cost of over $300 million and taking just over 1-½ years to complete, this new Major League Soccer stadium is home to the Columbus Crew soccer team and can seat 20,371 spectators, including 30 suites and 1,900 club seats.
This five-story stadium includes a wide variety of framing materials. On Level 1, the exterior skin of the building is fiber cement panels supported off CMU, precast walls and cold-formed framing. Wrapping around the entire building above Level 1 is a glass screen wall that is supported off massive 16”x12” HSS girts. Inside the building, the seating and steps are precast concrete and most of the walkable surfaces are concrete on metal deck.
Design Challenges and Solutions
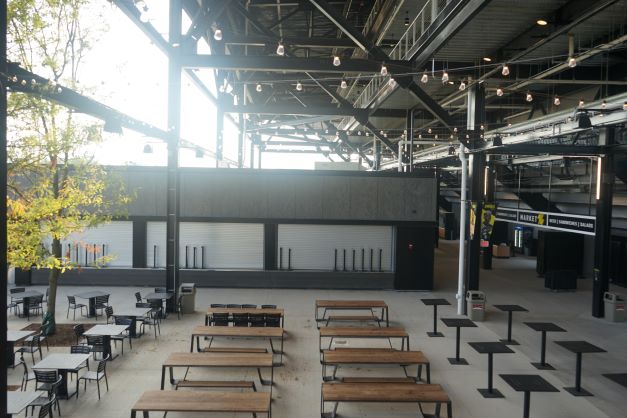
The challenges from a design standpoint came from all the interior building structures. This project was built during the height of the COVID-19 pandemic which caused many shortages from a steel standpoint. Many of the roof joists for these buildings could not be sourced, so the team utilized cold-formed metal framing (CFMF). Our client was also limited on the material available, so we worked with the engineer of record (EOR) to provide beam placement where needed to keep all the joist framing at 12” 14ga. Not only did these joists need to support typical dead, live, and snow loads, but they also needed to support heavy mechanical equipment and fall arrest posts that stood 48” above the roof surface. Many calls and plan iterations were undertaken to provide accurate joist layout and double joists where required to support the mechanical rooftop equipment. Custom-made baseplates were made for securement to the fall arrest posts to the roof joists. Most of these interior building structures were constructed entirely of cold-formed framing featuring cold-formed joists, load-bearing walls and X-braces for stability.
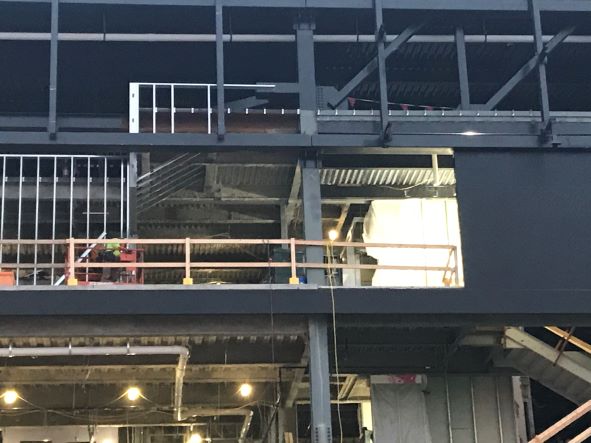
The project provided several construction challenges, but none larger than an entire floor of curtainwall that was shown to be supported off a smaller curtainwall system. The delegated designer for the glazing system was not able to use the smaller curtainwall system to support the larger system. At this point the slabs were poured and the steel was in place. Moving or cutting the structure out to provide a larger curtainwall at the base was not an option. Based on three years of experience as a glazing designer I offered up the idea to add cold-formed framing behind the spandrel glass to support it. Since it was spandrel glass, one could not see through it, so the framing behind the glass did not matter and the curtainwall pressure caps could still be screwed on at 4’-0” O.C., providing the same appearance desired by the architect. The idea was accepted, and the result was a structure that could support the larger upper curtainwall system without changing the aesthetics of the stadium.
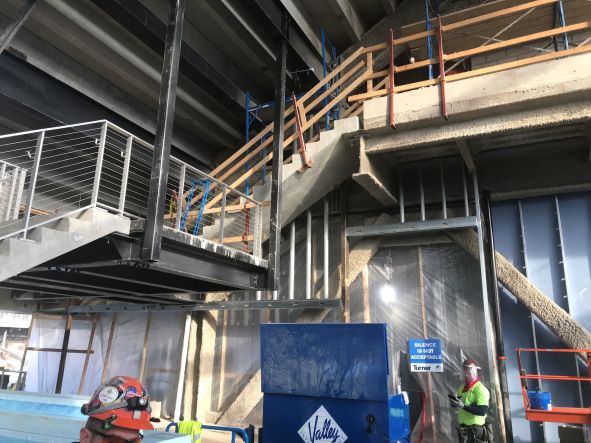
Along the west elevation of the stadium at the second floor was a band of exterior insulation finishing system (EFIS) that was supported off cold-formed framing. The cold-formed steel ran to the underside of the large 16”x12” HSS girts that supported the exterior screen wall. These HSS girts were not part of the structural scope of work and were provided by the glazing contractor. The girts were only designed to support the screen wall system and not the cold-formed steel. A custom bulkhead was framed around these girts and where possible, the exterior wall framing and bulkhead were supported off interior building structures that framed into this outside wall.
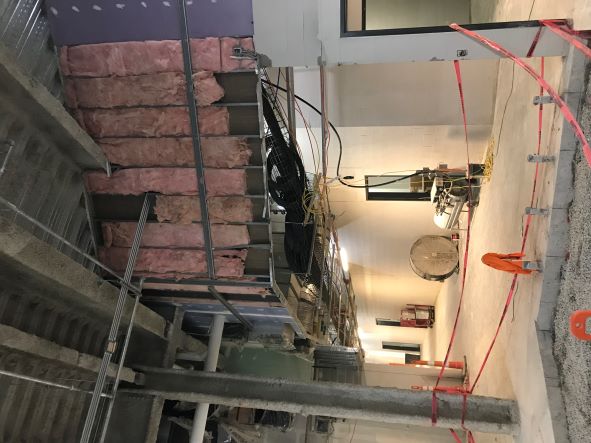
The last exterior challenge faced on this project was the large exterior soffits that ran under all the precast concrete seating and steps. Due to the large amount of rebar used in these stairs/steps, there were only a couple of locations where the soffits were able to be supported. Working with the precast designer, Excel designed strong-backs to carry the soffit load where needed and also designed the soffit members to have large cantilevers to meet the deflection and stress requirements of the cold-formed framing, as well as the attachment locations wanted by the precast designer.
The challenges did not not end once inside the interior buildings. There were large moment-framed bulkheads that cantilevered down 12’-0” from the structure above to catch large interior glazing systems. To support these bulkheads, large strongbacks were designed to span between beams, and the bulkhead then hung/kicked back to these strongbacks for support. Additionally, many of the bars in this stadium had liquor display shelving that needed to be hung from the structure above. Excel was tasked with designing the supports for these to be hidden in the ceiling above. Strong-backs were again used to span between beams and the shelving supports were hung and kicked back to these strongbacks as required.
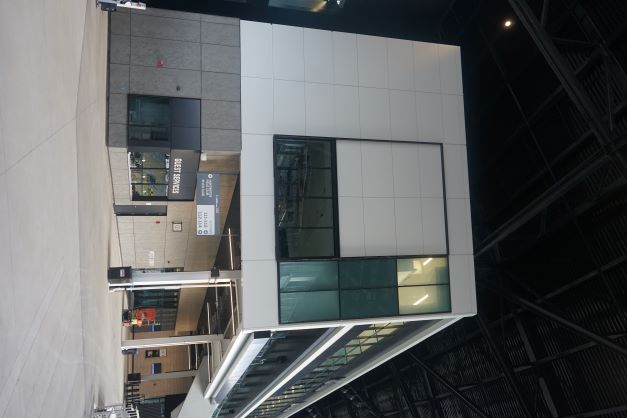
Designing a project of this size and complexity can be overwhelming, no matter the circumstances. Designing it during a worldwide pandemic where material and labor shortages were at an all-time high added another layer to an already complex project with a tight deadline. Constant communication with the design team on this project, coupled with creative thinking, allowed smooth and decisive solutions for what could have been extremely stressful and drawn-out challenges. The end result is a project and stadium everyone take pride in constructing.
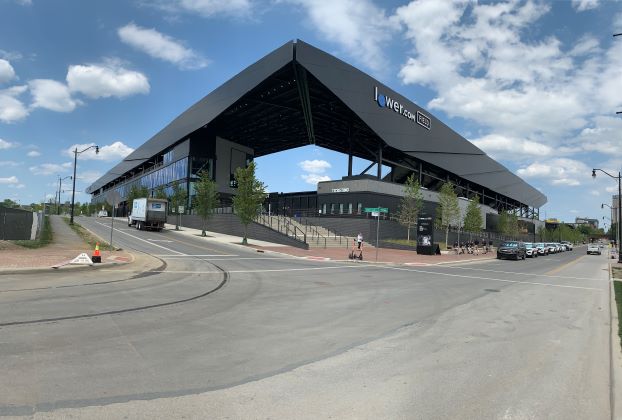
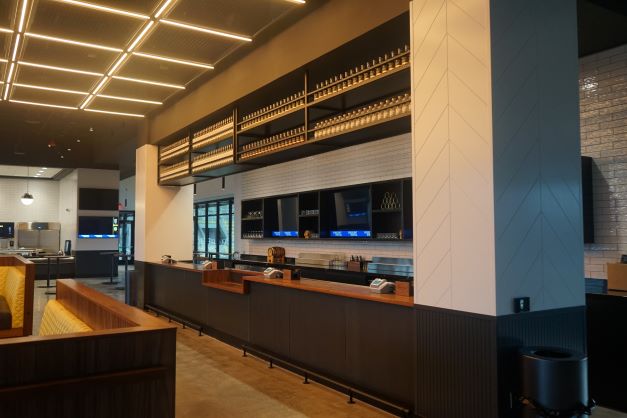
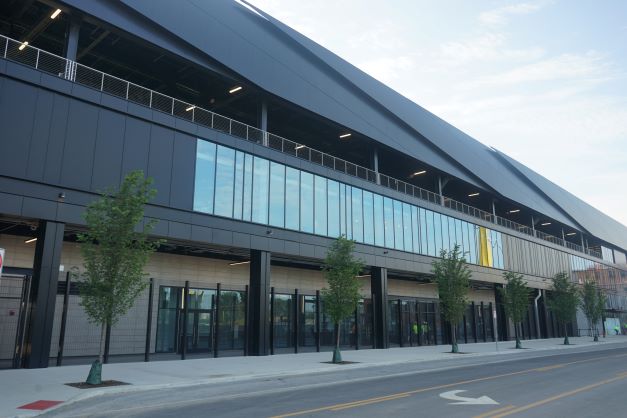
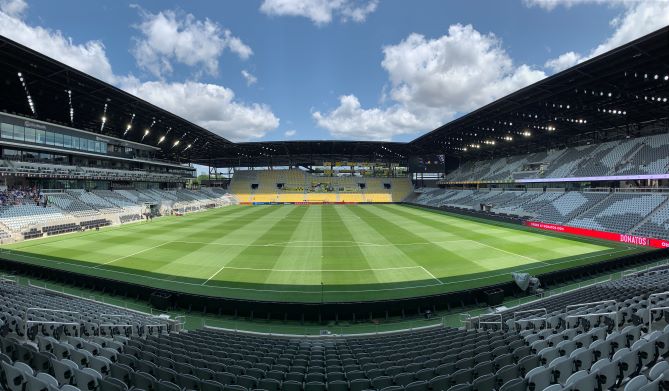
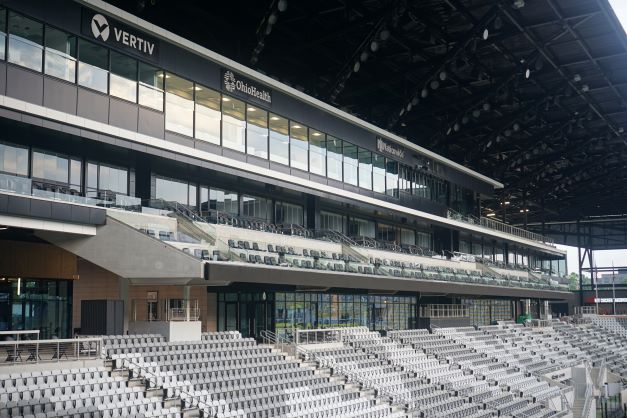
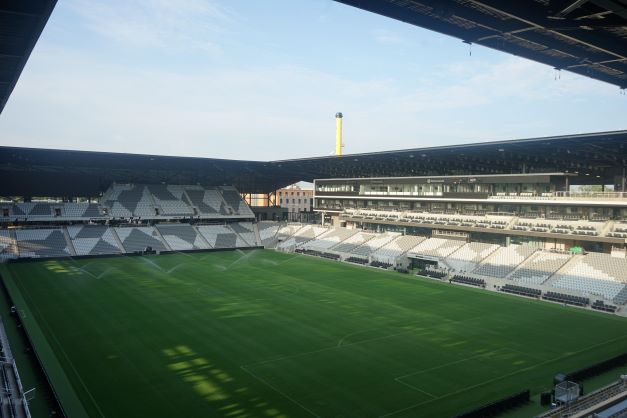
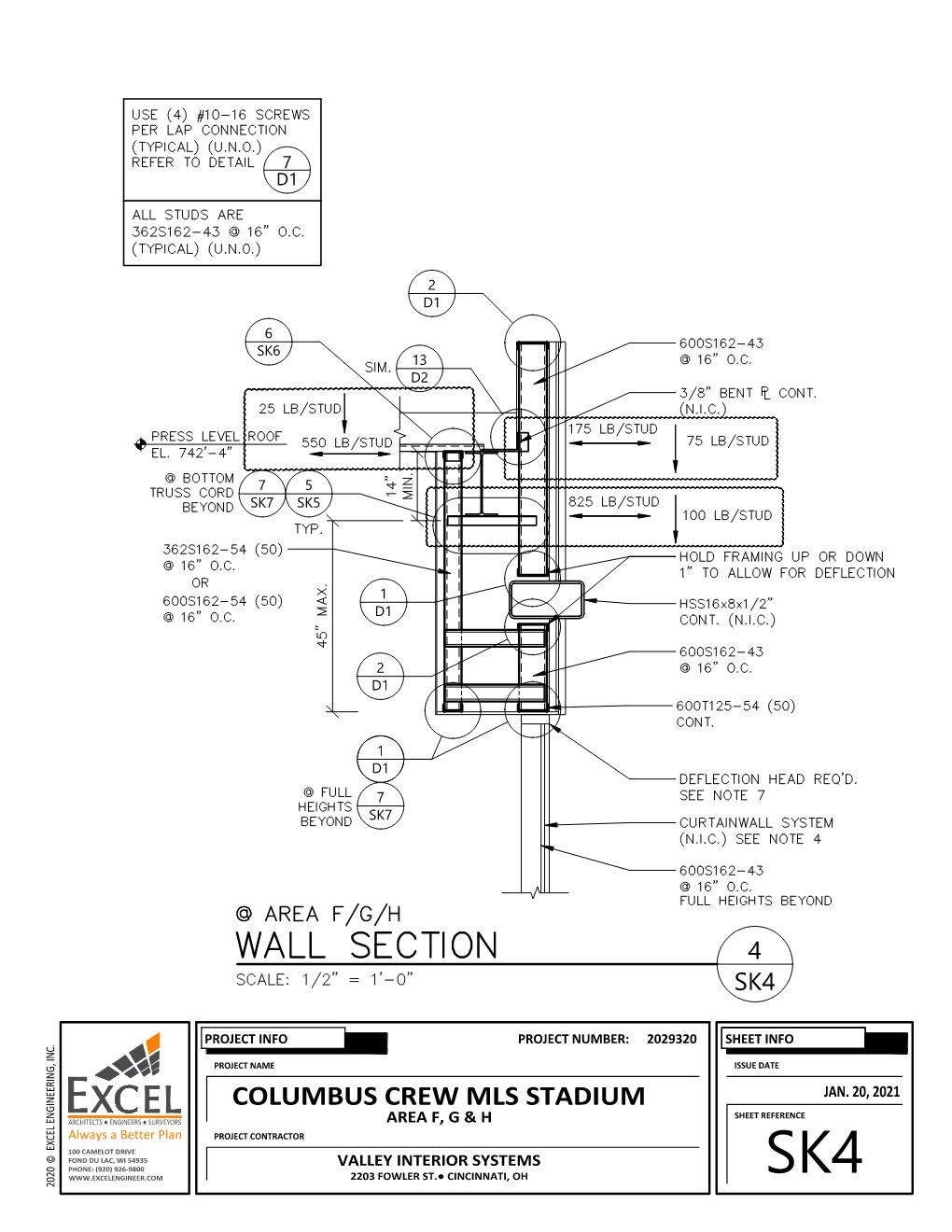
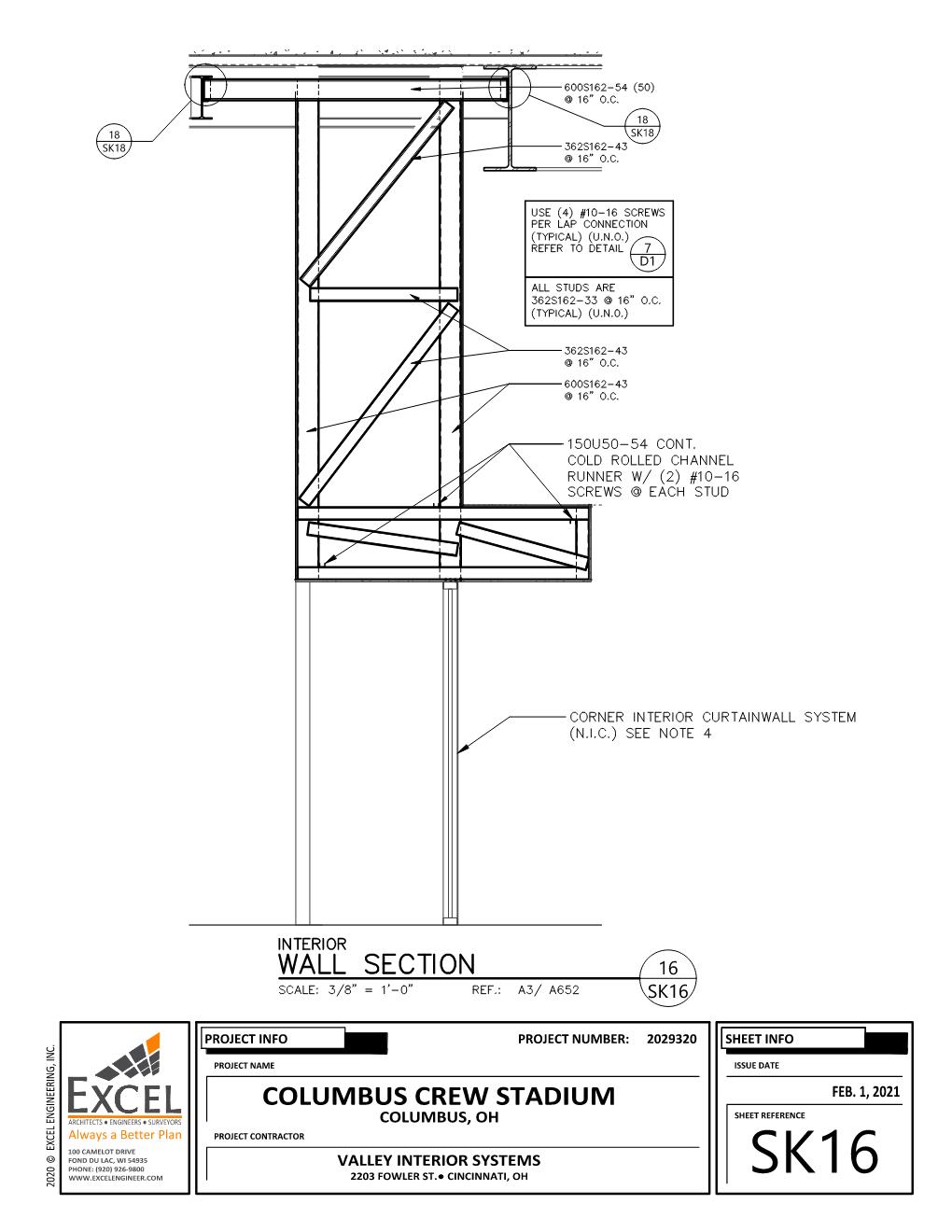
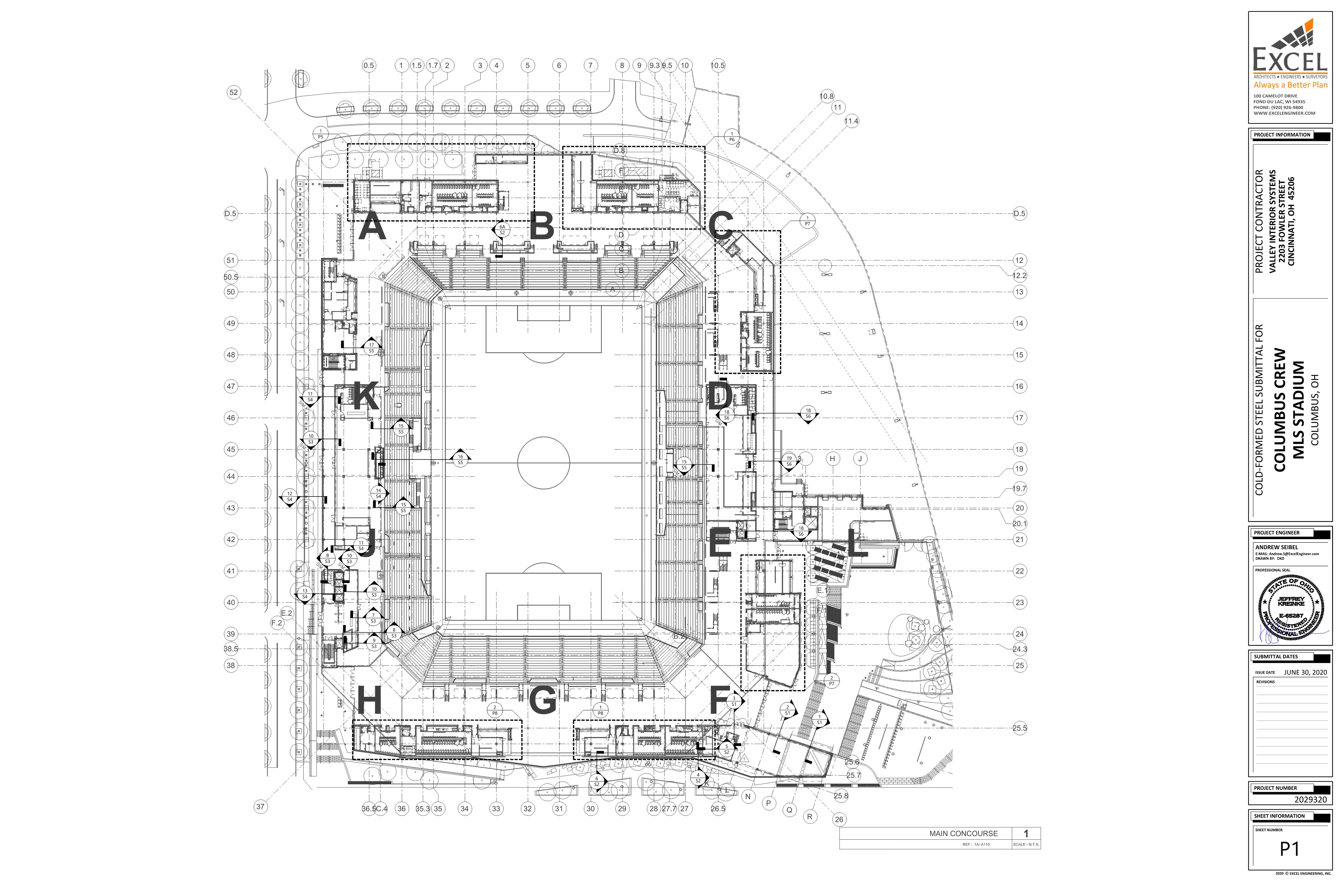
|