2022 CFSEI DESIGN EXCELLENCE AWARD WINNERS
FIRST PLACE – MUNICIPAL/CULTURAL
LOCHSA ENGINEERING, LLC – AUDREY IRMAS PAVILION LOS ANGELES, CALIFORNIA
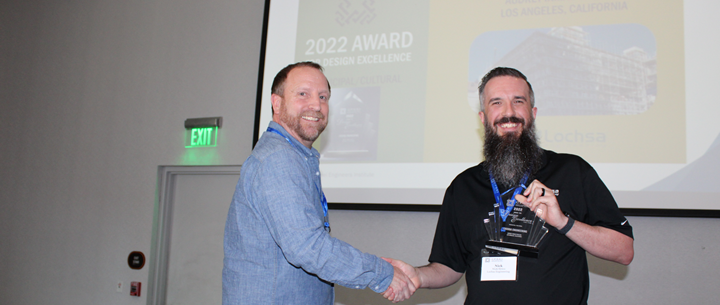
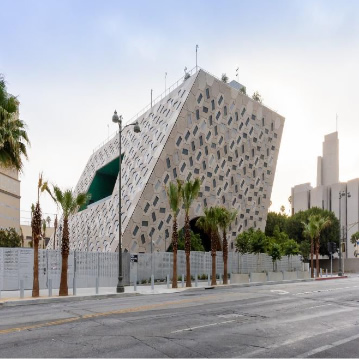
Audrey Irmas Pavilion 3643 Wilshire Boulevard Los Angeles, California 90010 Completed: September 2021 Construction Cost: $95 million
Owner: Wilshire Boulevard Temple Architect of Record: Zohar Sorek, AIA (Gruen Associates),Office of Metropolitan Architecture (OMA) / Gruen Associates Engineer of Record for Structural Work: Terry Zhang, P.E., Arup General Contractor: Matt Construction Cold-Formed Steel Specialty Engineer: Derrick Suarez, P.E., Lochsa Engineering, LLC Cold-Formed Steel Specialty Contractor: Tom Whittey, Performance Contracting Inc. (PCI) Award Entry Submitted by: Derrick Suarez, P.E. and Nick Hrico, P.E., Lochsa Engineering, LLC
Project Background
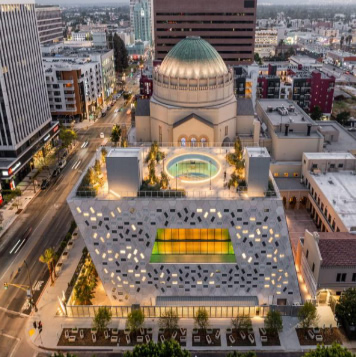
The Audrey Irmas Pavilion is named for its lead donor, Ms. Audrey Irmas, a philanthropist, art collector, native Angeleno, and longtime attendee of Wilshire Boulevard Temple. Her $30 million gift led the private funding of the new building, which completes Wilshire Boulevard Temple’s three phase master plan for the campus that spans the entire city block on Wilshire Boulevard, between Harvard and Hobart Avenues.
The Audrey Irmas Pavilion is a platform for gathering, a facility created for the community as an event and civic performance space, while simultaneously respecting historic traditions and reflecting modern needs. The 55,000-square-foot-structure was designed to be iconic enough for recognition as a new community space but understated enough to complement the existing temple.
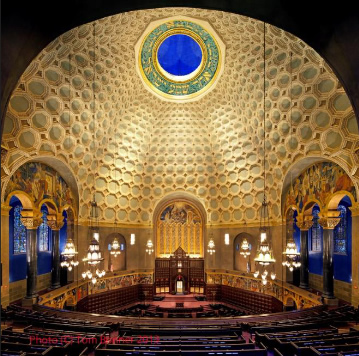
The project began as a box, a typical prototype for an event space. The basic box was then designed to be visually respective to the adjacent historical buildings on the campus. The west side of the building slopes away from the existing temple, surrounding a new courtyard between the two buildings. The pavilion leans south, away from the historic school, allowing for optimal light to enter the space, while the parallelogram simultaneously reaches out toward the main thoroughfare, Wilshire Boulevard. The resulting form of a building with four sides, only one of which is completely vertical, is both deferential and modern. The unique exterior incorporates elements from the geometry of the temple’s domed interior.
Event spaces often sacrifice beauty and character, for functionality. Through the ingenuity of the design team, the creative elements provide both character and functionality. There were multiple challenges to face and solve in order to achieve this successful project.
Design Challenges and Solutions
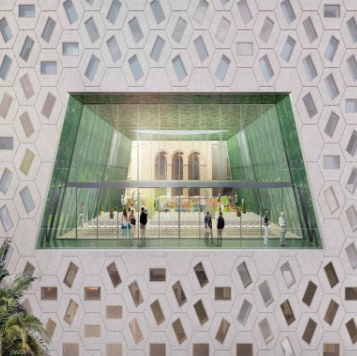
One of the first issues facing the project team was that the location of the project, which was the middle of a congested city and had only a minimal amount of laydown area. This meant traditional on-site stick framing was not a viable option. Lochsa Engineering worked with the cold-formed steel (CFS) contractor, Performance Contracting Inc., to come up with a solution to build the bulk of the exterior framing offsite. A standard panelized framing system was not feasible since the exterior walls had a large number of windows that were all angled in different directions. The solution was a panelized ladder framing concept that could span floor to floor and encompass the angled windows. The ladder framing could be constructed offsite, shipped to the site and erected. This would allow for better coordination of the complex angled windows within the GFRC hexagonal panels and reduce the number of connections back to the main structure.
Another issue faced by the project team was the architecturally sloped and skewed exterior walls. With only one of the four exterior walls being truly vertical, the connections back to the structure at the other three sloped walls had several design challenges. The wall framing was designed to bypass the slab edges, which added to the engineering challenges for the wall support(s). With the sloped walls came a greater edge of slab-to-framing distance which further complicated the connections to the structure.
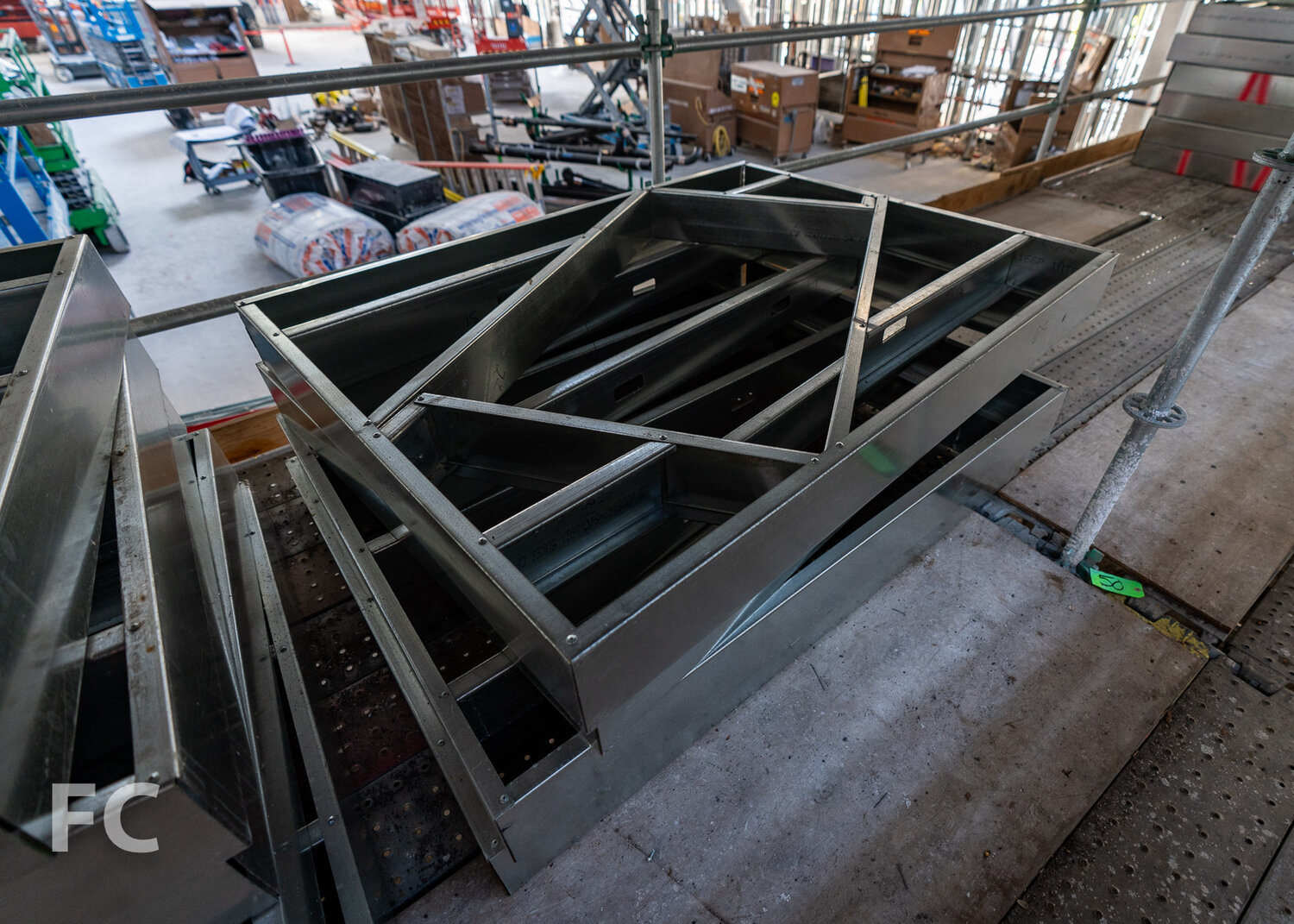
An additional challenge to overcome was the movements of the building during lateral events as well as the typical live load movements. The overall floor deflections were in line with industry standards but having the angled and skewed exterior wall framing posed some design challenges, compounded by designing for expected story drifts. Due to the drift requirements for lateral movement, the framing needed to be interrupted at each level to allow for the floors above to move independently of each other while also accounting for the vertical deflection. Since these exterior walls were sloped both inward and outward, standard drift and deflection clips were not an option due to the sloped walls and the distance from the support members, but the overall concept was still utilized. Specialized connection details at each floor, for each sloping exterior wall were created to achieve the desired results and span the distances to the supports.
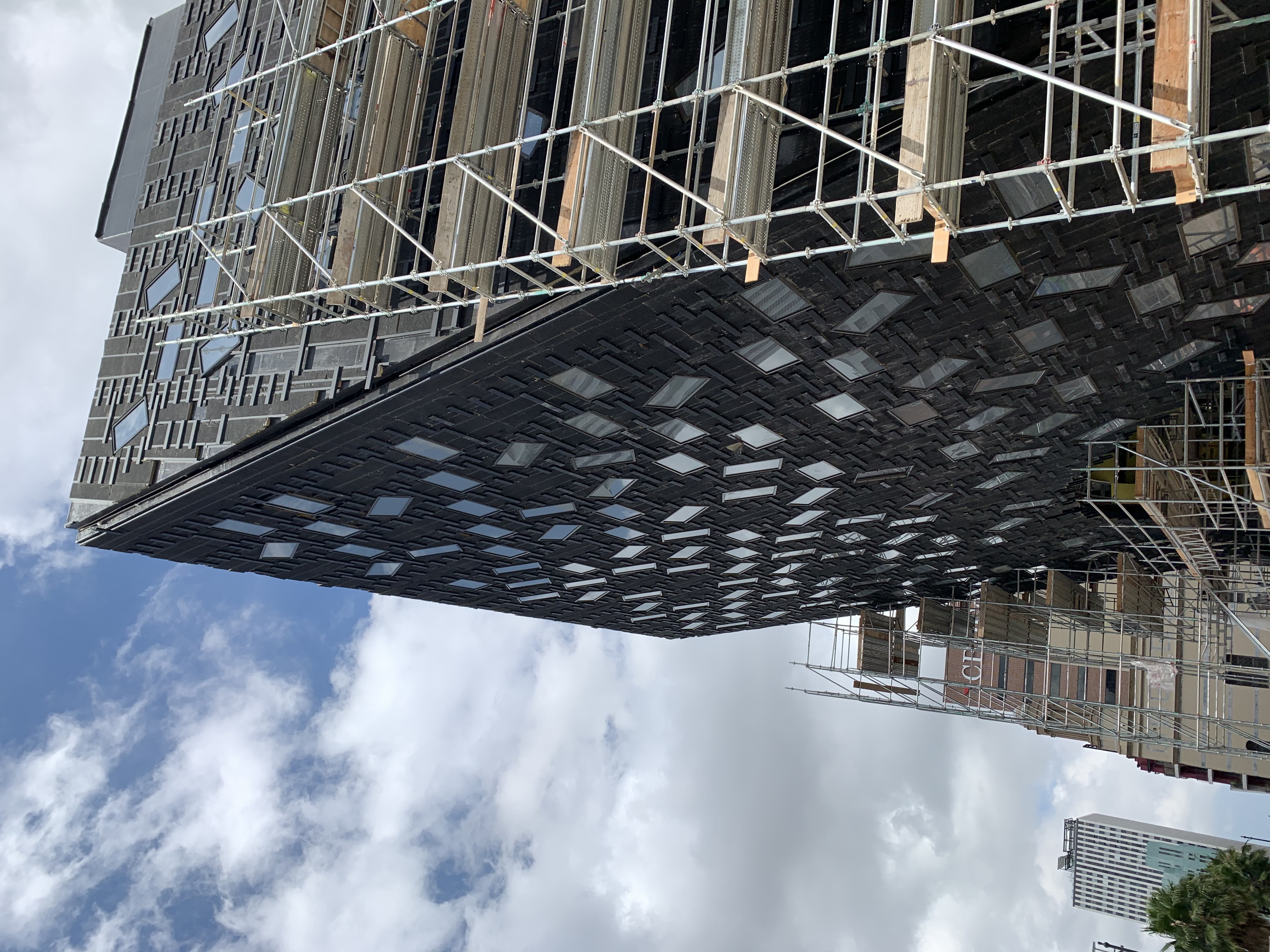
Due to the drift requirements, Lochsa Engineering needed to devise a solution to allow one side of the building to move without interfering and colliding with the intersecting walls. The CFS framing was held back at the corners (commonly called crush zones) which was made more difficult by having two intersecting walls that sloped in two different directions. Since the ladder framing was designed to span floor to floor vertically, the angled corners offered no structure to attach to, as it sloped outwardly.
The corners proved to be rather complex. A combination of heavy gauge CFS and structural steel frames were created to support the ladder framing and create the standoff needed at the corners. Hollow structural section (HSS) posts were designed and installed to receive a cantilevered HSS to provide support for the CFS framing at the gaps in the corners which allows the walls to pass by each other in a lateral event.
This project presented many challenging design aspects for both vertical and lateral movements in the exterior and interior framing and how to build them within the constraints of the site. The Lochsa Engineering team collaborated closely with the CFS framing contractor to work through several options and ideas and build mockups of the framing system to create these options. As difficult as this project was, in both design and construction, the finished product speaks for itself and is a beautiful addition to the site.
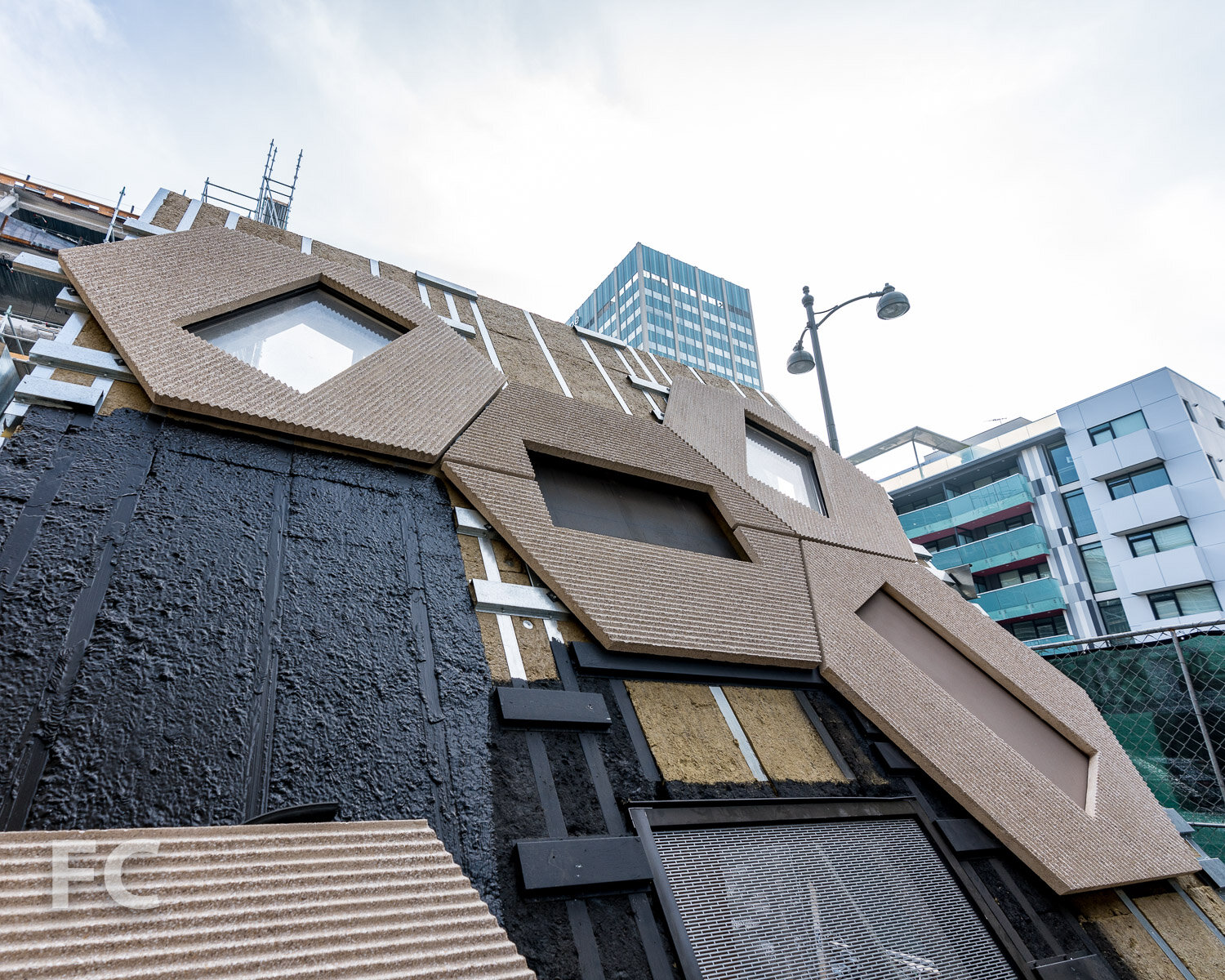
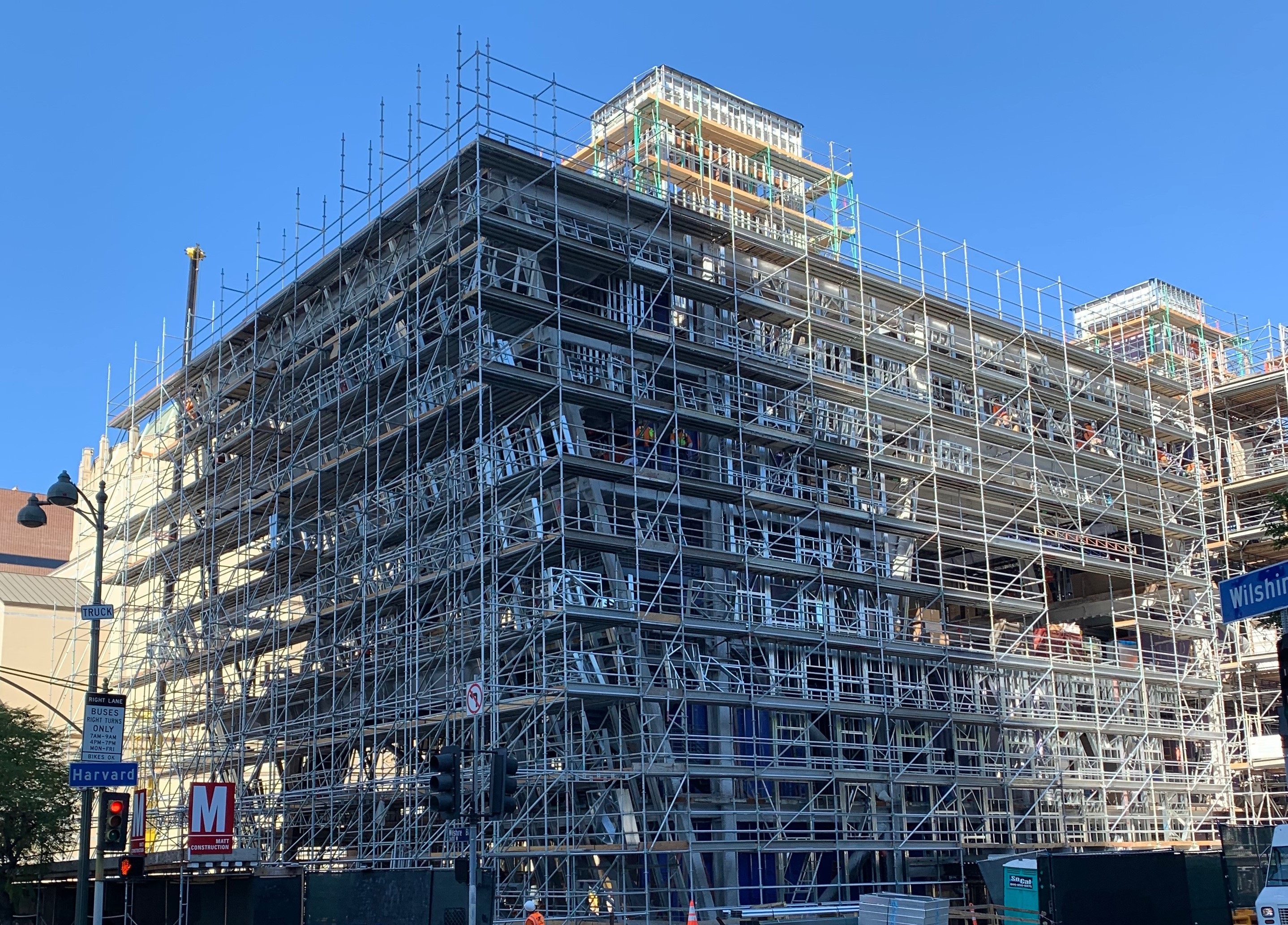
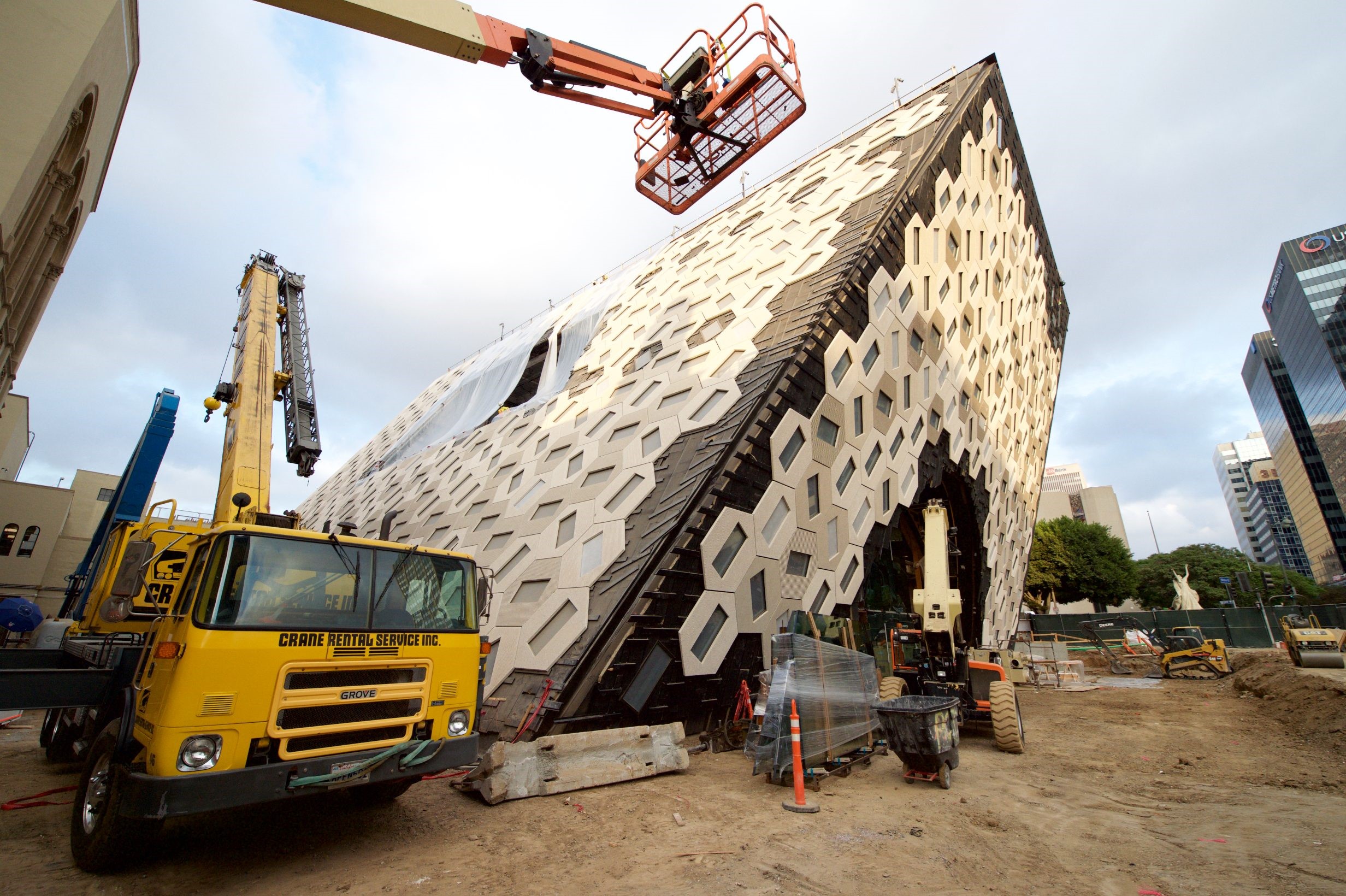

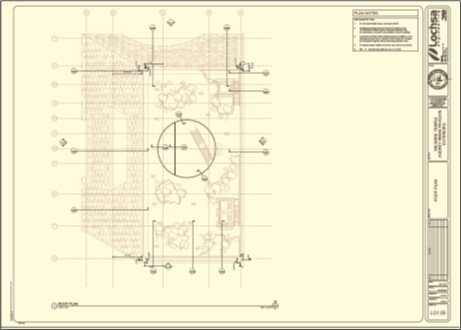
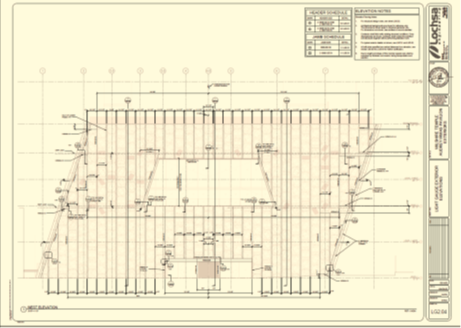
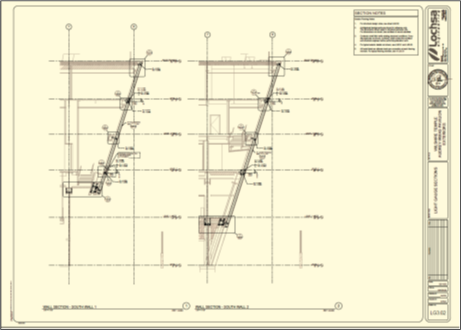
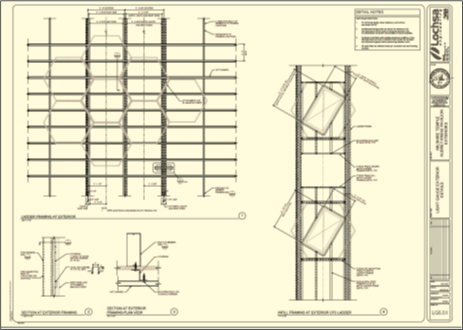
|