2024 CFSEI DESIGN EXCELLENCE AWARD WINNERS
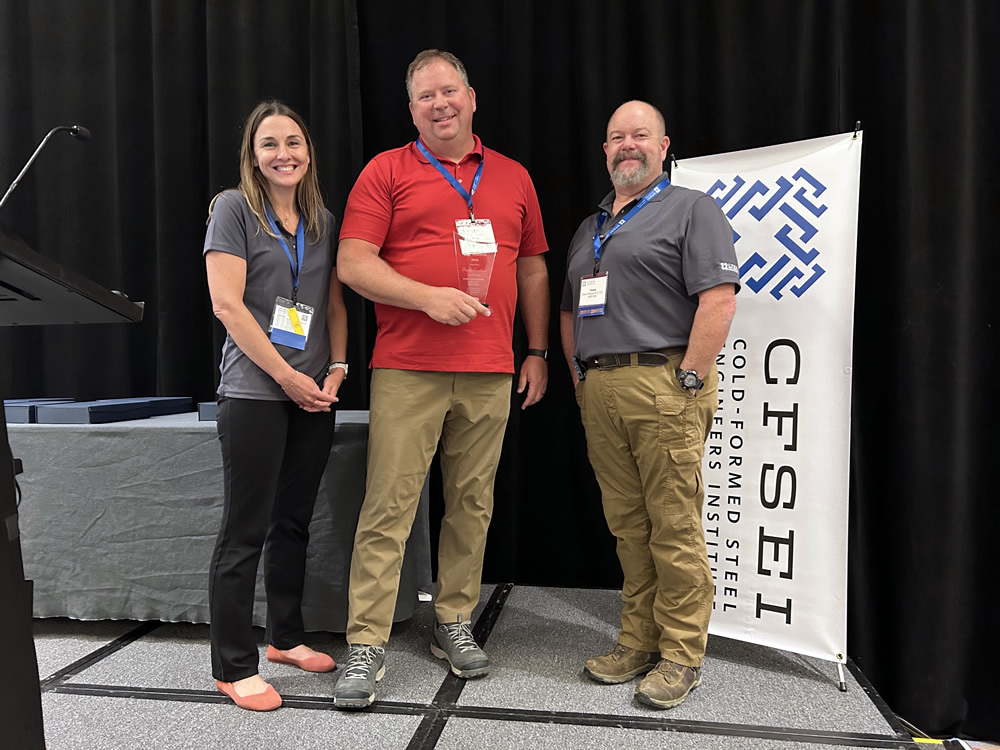
SECOND PLACE
ENSIGN ENGINEERING AND LAND SURVEYING THE SPHERE AT THE VENETIAN RESORT LAS VEGAS, NEVADA
The Sphere at the Venetian Resort 255 Sands Avenue Las Vegas, NV 89169
Completion Date: September 2023 Construction Cost: 2.3 Billion
Owner: The Madison Square Garden Company. Architect of Record: Populous. Engineer of Record for Structural Work: Severud Associates Consulting Engineers. Cold-Formed Steel Specialty Engineer: Alex Hawkins, P.E., S.E., Ensign Engineering and Landing Surveying. Cold-Formed Steel Specialty Contractor: Carissa Wood, KHS&S Contractors. Award Entry Submitted by: Scott Roche, Ensign Engineering and Landing Surveying.
Project Background
The MSG Sphere at The Venetian hotel in Las Vegas is a unique venue aimed at transforming the way that audiences experience concerts and visual events. It is billed as the “Largest Spherical Structure” in the world. The structure rests on a “Collar” that has a twisted surface that curves around the base of the building.
The unique geometry of the EIFS collar required custom engineering and detailing specific to the structure. The prefabricated, panelized, cold-formed steel (CFS) stud structure provided the perfect solution for the collar. The panels required precision design and fabrication to ensure structural integrity and a seamless installation.
Design Challenges and Solutions
The geometry of the EIFS collar around the base of Sphere is anything but regular. You can think of it as a section of a skewed cone. The wall leans constantly away from the building on a reverse slope. As it wraps around the building, the collar changes in height, radius, and slope. This means that nearly every panel is unique.
The structure for the EIFS collar is made up of custom, panelized, steel stud walls attaching to the concrete and steel structure by others. There are also about 3 bays where we designed a cold-formed steel (CFS) main structure for the EIFS wall to attach to. For these 3 bays, cold-formed steel (CFS) makes up the bearing walls, the lateral system, the EIFS walls, the roof deck, and even the roof trusses. Cold-formed steel (CFS) provided the strength and versatility required to meet the demanding requirements for collar construction.
Scott Mitchell and his team at STUD-IO analyzed the geometry to determine the precise geometry of each panel. The 142 panels vary significantly, with widths between 6 and 9 feet, the tallest panels being about 38 feet tall, and the most significant slopes being nearly 15 degrees from vertical.
Each panel is wider at the top than it is at the base. Machine fabrication was critical in producing the complex geometry. A Howick machine cut, punched and labeled the pieces.
Then, nearby in Las Vegas, KHS&S assembled the pieces to create each panel. The sheathing, foam and stucco were applied off-site before the panels were shipped to the base of Sphere.
While other materials were considered, cold-formed steel (CFS) was selected because it was light weight, cost effective and allowed for machine fabrication. Building the panels off-site decreased on-site construction time by allowing panels to be fabricated concurrent with other construction. It also improved on-site safety by reducing the time workers spent in elevated areas.
The use of the Howick machine reduced material waste because each piece was fabricated to a precise length. Finally, the panelized approach improved accuracy and efficiency by fabricating panels in a controlled environment.
he complex geometry, combined with the panelized construction, required engineering that ensured accuracy and accommodated the off-site construction.
One unique design aspect of the design was the custom detail at the base of most panels. The base of the EIFS wall is up to 15 inches away from the concrete foundation, meaning that the connection had to accommodate a significant cantilever and support the gravity load from panels up to 38 feet tall. The typical detail for such a condition would likely employ a continuous ledger angle. However, the circular footprint of the building would not allow for such a solution. In addition to the structural requirements of the connection, it was critical that the connection allow the geometry to be defined by the model to ensure accuracy in the final product.
Ensign Engineering coordinated with KHS&S Contractors and STUD-IO to develop a detail that met the structural and constructability demands. The finalized detail utilized a handshake connection between two steel studs. The angle between the two studs was defined by the model and the studs were custom fabricated using the Howick machine.
The pre-punched holes from the Howick provided the precise geometry needed for each connection. Instead of a continuous ledger, short ledgers were spaced 3 to 4 feet apart, and a heavy gage angle was provided on the panel to support the steel studs and span between the ledgers.
The finalized detail ensured that each panel sloped correctly and aligned with the adjacent panels as the construction wrapped around the building.
Similar solutions were developed in other areas, including the loading dock, where panels were suspended at their tops rather than being supported at their base.
 Photo Courtesy of Ensign Engineering & Land Surveying |
|
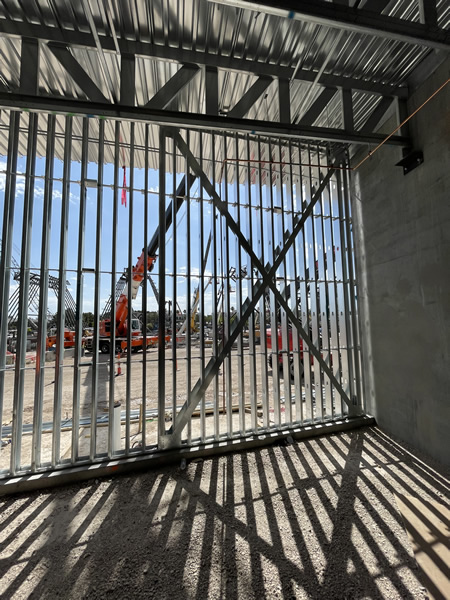 Photo Courtesy of Ensign Engineering & Land Surveying |
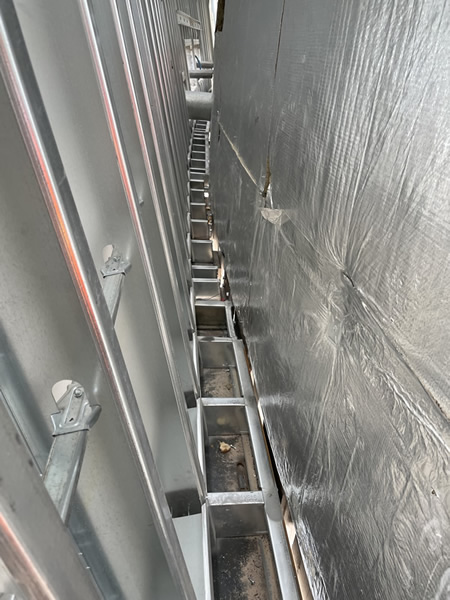 Photo Courtesy of Ensign Engineering & Land Surveying |
|
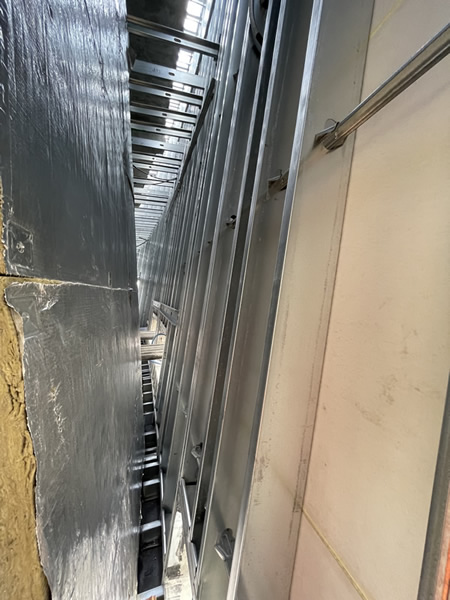 Photo Courtesy of Ensign Engineering & Land Surveying |
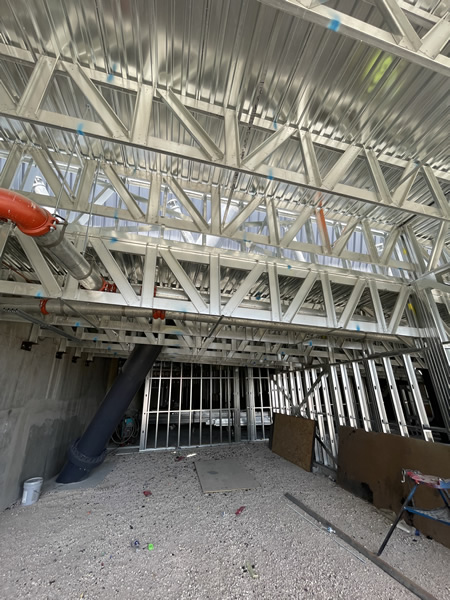 Photo Courtesy of Alex Hawkins, P.E., S.E.
|
|
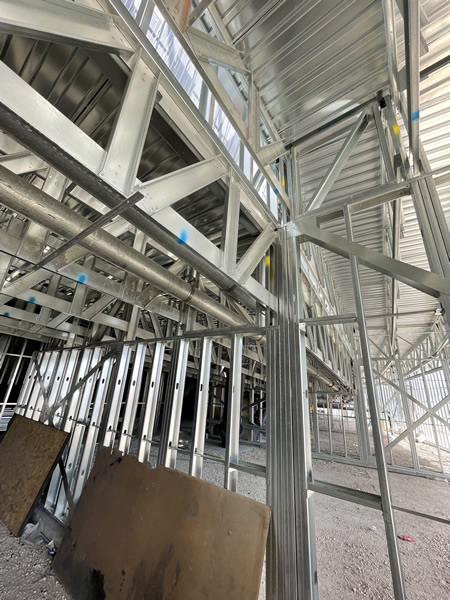 Photo Courtesy of Alex Hawkins, P.E., S.E. |
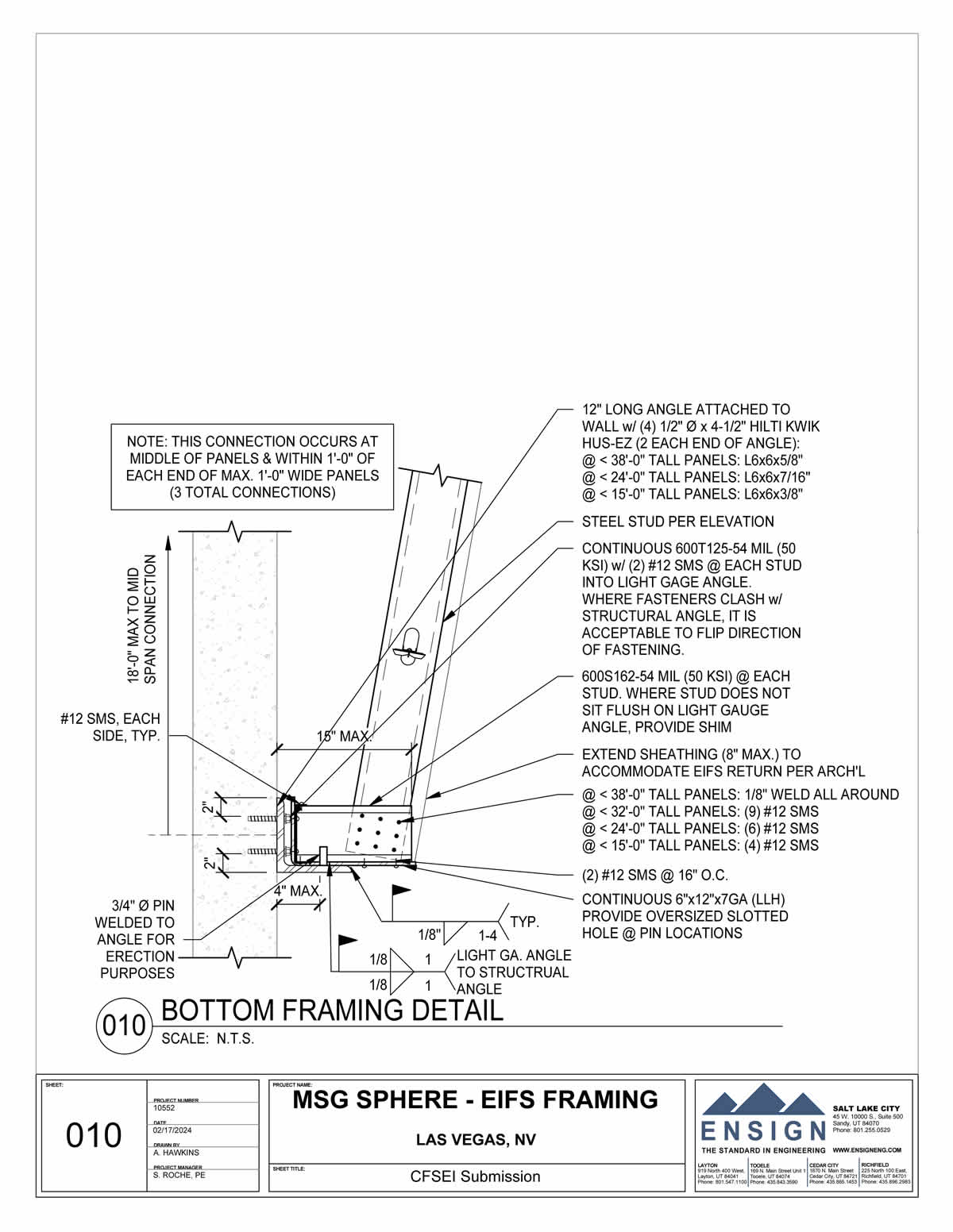
|