2015 CFSEI DESIGN EXCELLENCE
AWARD WINNERS
SECOND PLACE
DSi ENGINEERING, LLC – ELAN WESTSIDE APARTMENTS
ATLANTA, GA
Elan Westside Apartments
691 14th Street
Atlanta, GA 30318
Completed: April 2014
Construction Cost: $45 million
Owner: Greystar Apartments
Architect of Record: Surber Barber Choate & Hertlein
Engineer of Record for Structural Work: Sergio LeGuizamon, Browder + LeGuizamon & Associates, Inc.
Cold-Formed Steel Specialty Engineer: Steve Haddad, DSi Engineering, LLC
Cold-Formed Steel Specialty Contractor: Mitch Hughes, DSi Structures, LLC
Project Summary:
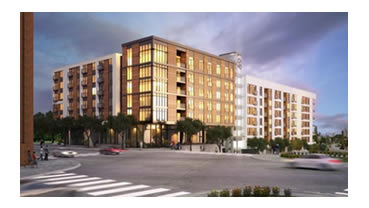
Elan Westside, the burgeoning West Midtown neighborhood at the corner of Howell Mill Road and 14th Street in Atlanta, GA is an eight-story building with 197 apartments and 11,000 square feet of retail space perfectly suited for cold-formed steel construction. Each apartment boasts state-of-the-art amenities. Residents of Elan Westside enjoy several amenities on the property including a fitness center with virtual trainers, a first-class saltwater pool, an entertainment lounge and clubhouse with multiple high-definition televisions, and a bar and cyber café offering various video game consoles.
Elan Westside provides an incredible example of the efficiencies and constructability of cold-formed steel construction. The building includes six stories of load-bearing cold-formed steel framing on top of two levels of concrete parking structure.
Construction was already well underway when DSi Engineering was contacted about the project, so the contractor was not only concerned about costing, but also desired to provide a high-quality product for his customer in an amazingly short timeframe. When the client learned about DSi’s ability to create a single innovative Building Information Modeling (BIM) model that provided structural framing drawings, layout drawings, shop drawings and material rolling information, he became intrigued. With little delay, DSi was selected to provide and build the entire cold-formed steel structural assembly above the concrete transfer slabs.
Within just six weeks, the structural design and drawings were nearing completion and materials were being prepped for order. Within 12 weeks, materials were being fabricated, and in less than four months, materials were being erected. The entire project only took 18 weeks to build, much of which involved installation of the complicated and large trussed roof.
This project required a combination of welded, pre-panelized load-bearing cold-formed steel walls, structural steel, and dovetail composite deck supporting a floor slab. The roof was made up
of pre-engineered cold-formed steel trusses. To expedite the speed of construction, the project was divided into three phases per floor. This approach allowed walls to be erected in one phase, while flooring was installed in another, and shoring and concrete pours occurred in the third. The project superintendent commented, “I love this panelized wall system. It’s really good quality and goes up so fast, while keeping my job site clear and clean.”
Download Case Study 