2025 CFSEI DESIGN EXCELLENCE AWARD WINNER
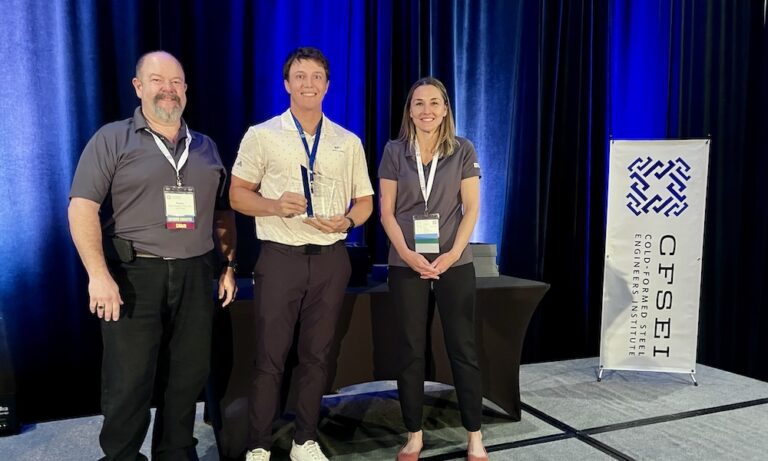
THIRD PLACE - RESIDENTIAL/HOSPITALITY
McCLURE - NINE31 APARTMENTS GAINESVILLE, FLORIDA
Nine31 Apartments 931 University Avenue Gainesville, Florida 32601
Completion Date: 2024 Construction Cost: $48 Million
Owner: CA Ventures. Architect of Record: Pierangeli Simonpietri AIA, NCARB, Dwell Design Studios. Engineer of Record for Structural Work: Daniel Roux, P.E., S.E., E&M Structural, Luis Hasbun, P.E., E&M Structural. Cold-Formed Steel Specialty Engineer: Jesse Barnes, P.E., S.E., McClure, Marcus Himmelberg, P.E., McClure. Cold-Formed Steel Specialty Contractor: Bruce Schierding, Eisen Group. Award Entry Submitted by: Lauren Gutknecht, McClure.
Project Background
The building at 931 University Aven, Gainesville, Florida, is a 10-story CFS structure above a 3-story concrete podium. The project was underway when McClure got involved. The podium construction was completed, but there were construction quality issues. The original CFS subcontractor and design were over budget and removed. McClure came in as the specialty engineer for a CFS system with a fast-paced schedule.
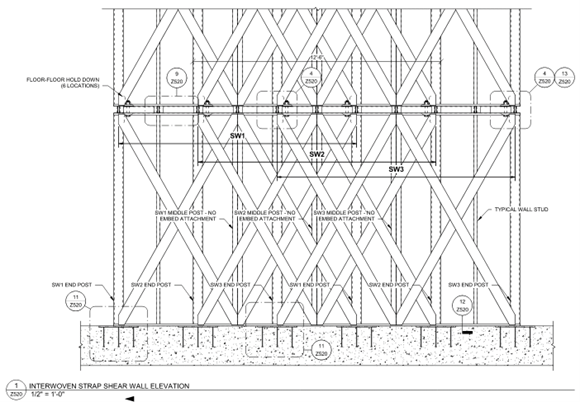
Design Challenges and Solutions
Several design challenges were brought up before the design process started. Embeds were already installed for lateral reactions and uplifts in the podium. The new design had to use the existing embeds, while keeping the uplift reaction under a design load of 50 kips to prevent the existing podium structure from exceeding capacity.
The existing podium was a PT concrete structure, so post-installing embeds were not feasible. Even when utilizing as many embeds as possible with almost every long run of useable shear wall, maintaining reactions of under 50 kips proved to be impossible.
Overlapping shear walls were required to reduce the reactions to maintain the existing embed limitations. This was modeled with a rigid diaphragm using relative stiffnesses to properly distribute the load to the stiffer shear wall locations. This was an iterative process that required several rounds of adding and removing walls to spread the reactions evenly to existing embeds. At the end of the analysis, some embeds were used, while others were not. Most reactions ended up being well below the 50 kip threshold while some remained near the limit.
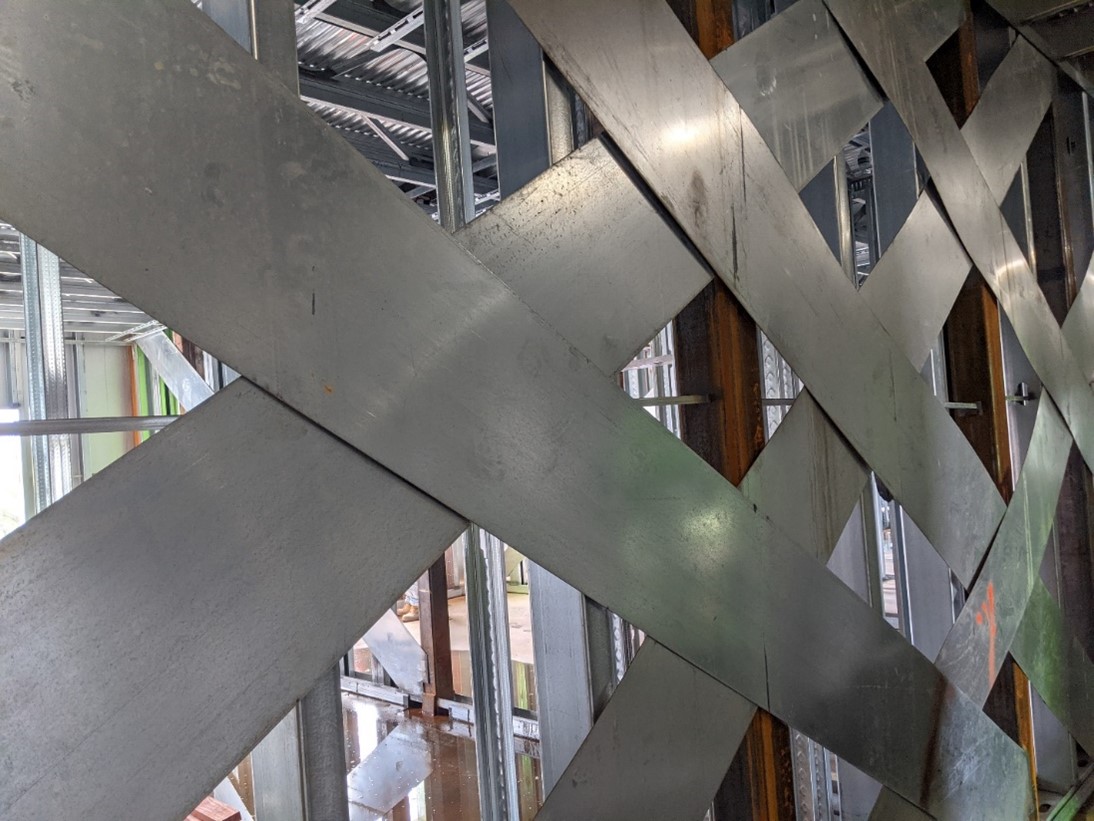
The second complication, and more problematic issue, was that the podium slab was known to be unlevel and not flat. The extent of the slab issues was not initially revealed to McClure. It was discovered later, from a survey, that the slab was not only poor in isolated locations but was in fact out of level from one end of the building to the other.
To determine the extent of this issue McClure was hired to do a 3D survey of the podium slab before any continued work above the podium on the building. The survey heat map showed that the PT concrete slab was 3” out of level from one end to the other, with varying degrees of elevation throughout the entire slab. A solution was needed to provide a proper bearing for a CFS bearing wall system that had to be fixed to near level and meet the standard 1/8” tolerance required for CFS bearing conditions.
Typically, this would be done with a topping slab or “leveling slab.” However, the EOR was concerned that this would provide too much additional weight to the structure. At 3” this would have been as much as 40psf additional dead load in some areas of the podium slab. McClure was challenged with finding a way to provide a level-bearing surface for the panel to sit on. The solution was an oversized track that allowed for placement of the walls and provided formwork for a flowable grout that could provide full bearing under the panels. (Figure 1)
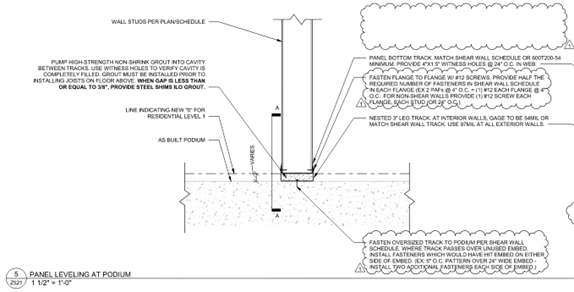
- Step 1: Layout the walls with the oversized tracks and install fasteners to the slab for shear as required.
- Step 2: Provide wood shims as required to level for setting of the bearing wall panels within the oversized tracks (Shims were placed between wall studs of the panels to allow for full bearing of the gravity load after Step 4 was completed)
- Step 3: Fasten the wall panel to the oversized track with screws flange to flange.
- Step 4: Install flowable non-shrink grout through holes provided in the panel bottom tracks until full to provide adequate support for the wall panels. Note that shims were permitted for small gaps where there were concerns that the grout would not adequately flow under the bearing studs.
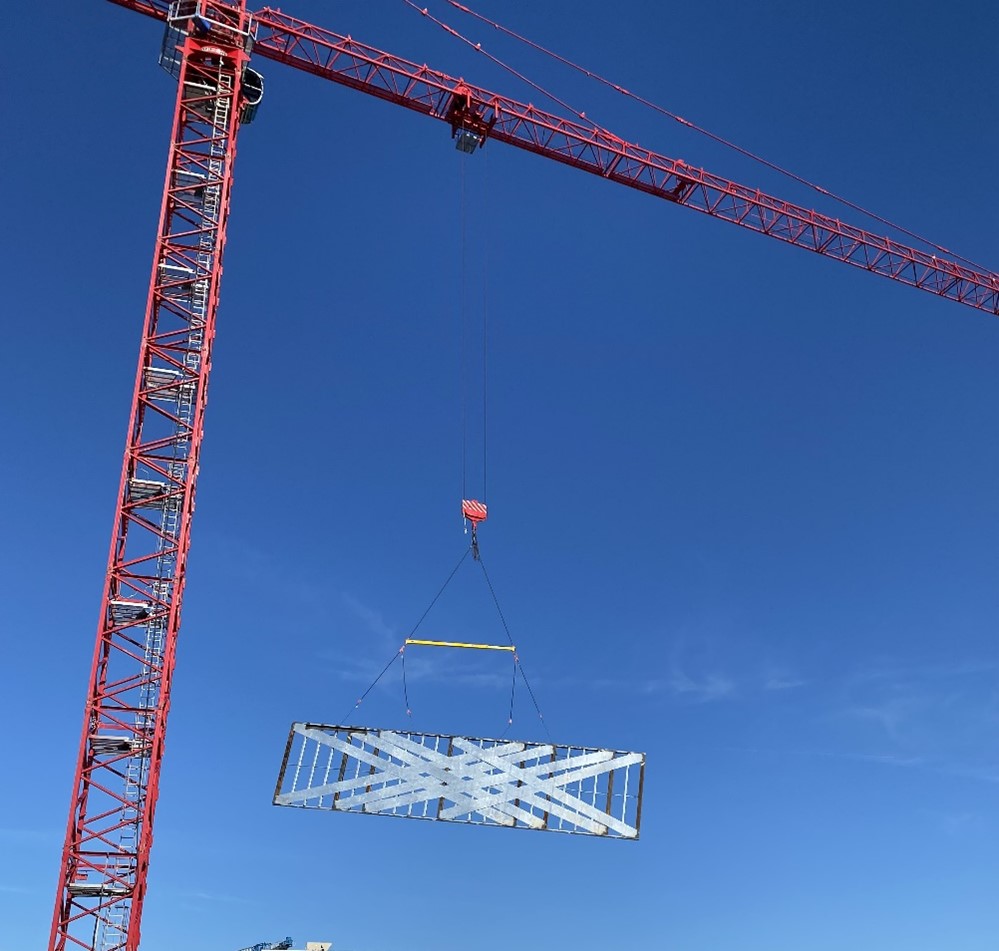
After construction began, additional issues emerged. Fortunately, a 3D scan had already indicated that some of these problems were likely, allowing McClure to prepare accommodating details in advance. In some cases, shear wall end posts did not align directly with the installed embeds. Elsewhere, bearing walls were found to overhang slab edges by as much as 3 inches. McClure collaborated with the EOR to develop solutions for these conditions. Additional steel was installed to support the bearing walls and provide a continuous load path to the embeds, preventing overstress beyond the allowable limits established for each shear wall end post.
McClure worked closely with the design team and contractors to engineer and detail numerous solutions that saved a project at risk of being incompletable. The existing conditions required the development of many specific details. McClure analyzed the existing shear wall force plan, performed 3D scanning of the podium structure, and designed never-before-used details for CFS load-bearing wall panels. Using an iterative approach, the team developed methods to reduce embed forces, created overlapping shear wall details, and introduced a new installation technique for load-bearing CFS panels on an unlevel podium slab. Without McClure’s problem-solving and cold-formed steel expertise, the Nine31 Apartments structure could not have been built.
.png)
|