2025 CFSEI CREATIVE DETAIL AWARD WINNER
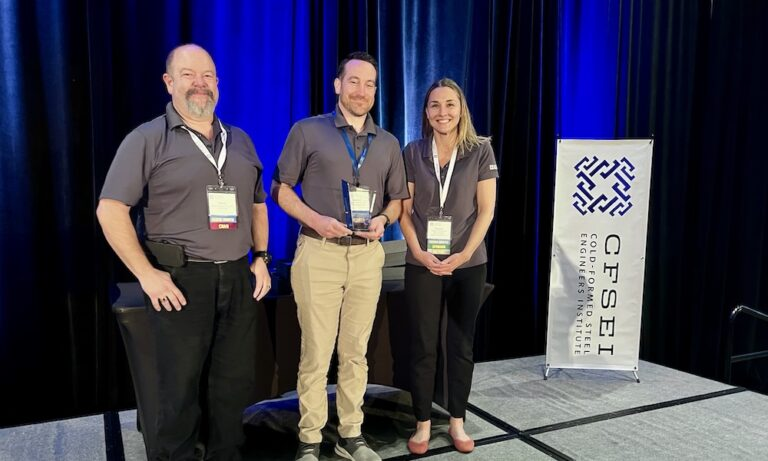
THIRD PLACE
ADTEK ENGINEERS, INC. - PULLER VETERANS CARE CENTER WARRENTON, VIRGINIA
Puller Veterans Care Center 6951 Vint Hill Parkway Warrenton, Virginia 20187
Completion Date: November 2024 Construction Cost: $68 Million
Owner: Department of Veterans Services. Architect of Record: Tom Payton, Orcutt|Winslow. Engineer of Record for Structural Work: James Harner, Wiley|Wilson. Cold-Formed Steel Specialty Engineer: Andrew Newland, P.E., ADTEK Engineers, Inc. Cold-Formed Steel Specialty Contractor: David Leutbecker, Pillar Construction. Award Entry Submitted by: Andrew Newland, P.E., ADTEK Engineers, Inc.
Project Background
Puller Veterans Care Center, a facility in Fauquier County, Virginia, has 128 rooms arranged in 16-room households, with a chapel, activity rooms and secure courtyards. Named after Marine Lt. Gen. Lewis B. "Chesty" Puller, the facility uses panelized cold-formed steel (CFS) walls, supporting CFS roof trusses, as its main structural framing. The main lateral force resisting system is x-braced CFS walls. Limited structural steel and decorative mass timber were also included.
Design Challenges and Solutions
Construction began in 2017. Once the main structural elements had been completed and installed and with sheathing and veneer in place, installation of the interior door frames began. At this time, the project team discovered the rough openings were too small to accommodate the door frames.
Prior to consulting the original specialty engineer, the specialty contractor began modifying the openings to fit the doors. After this was done, the original specialty engineer was contacted to provide repairs for the affected openings. Once limited repairs were done, ADTEK Engineers was contacted to perform a review of the repairs and repair details. Upon visiting the site, numerous deficiencies were discovered.
During drywall removal and remediation, numerous load-bearing wall stud flanges were discovered to be damaged beyond repair. Box beams had been used as load distribution members (LDMs) but proved insufficient to resist web crippling. At this stage, ADTEK was brought in to provide LDM repair and shoring details to extend the openings and meet rough opening requirements. In most cases, drop ceilings allowed strongbacks to be attached to the LDMs and remain in place as the new headers. Where this approach wasn’t feasible, 0.118 mil gussets were installed to reinforce the LDMs.
Opening 1008 presented several challenges. Because the LDM was not located at a drop ceiling, both a gusset reinforcement and a separate temporary strongback were required. Complicating matters, the opening was adjacent to an X-brace wall. The wall post had been designed to serve double duty as the jamb post with the addition of a single stud, which was damaged beyond repair. Since the shear wall post could not be altered, a unique shoring solution was necessary.
After reinforcing the LDM, strongbacks were installed on both sides of the wall. Their flanges were coped at the shear wall, and the webs fastened to the X-brace wall post. To avoid transferring additional load to the post, new full-height studs were installed on each face and clipped to the strongback. Once in place, the header and damaged jamb stud were removed and replaced with a new jamb stud. The temporary studs and strongbacks were then removed, allowing the wall and opening to be finished.
|