2025 CFSEI DESIGN EXCELLENCE AWARD WINNER
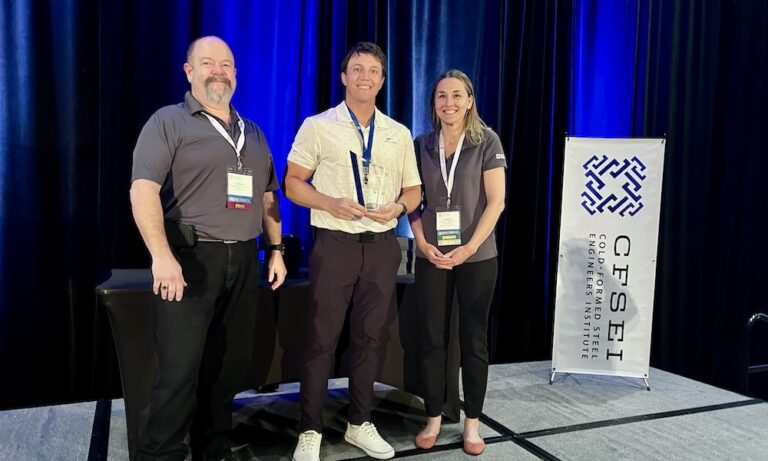
FIRST PLACE - MUNICIPAL
MCCLURE – MALACHOWSKY HALL FOR DATA SCIENCE AND INFORMATION TECHNOLOGY GAINESVILLE, FLORIDA
Malachowsky Hall for Data Science and Information Technology 1889 Museum Road Gainesville, Florida 32606
Completion Date: 2023
Construction Cost: $150 Million
Owner: University of Florida. Architect of Record: Bohlin Cywinski Jackson. Engineer of Record for Structural Work: Walter P. Moore. Cold-Formed Steel Specialty Engineer:Josh Garton, P.E., S.E., McClure. Cold-Formed Steel Specialty Contractor: Paul Wolmarans, Kenpat. Award Entry Submitted by: Lauren Gutknecht, McClure.
Project Background
The University of Florida’s Malachowsky Hall for Data Science and Information Technology in Gainesville, Florida is a standout example of innovation. The eight-story facility features more than 170,000 square feet of exterior cold-formed steel (CFS) non-bearing panels, built through a highly collaborative effort by McClure, Kenpat, the panel fabricator and installer and N-RG Cladding.
The team coordinated the design and construction of a fully prefabricated enclosure system, integrating 3D volumetric modular cladding panels with CFS wall panels. To enhance installation efficiency, the panels are secured to the concrete-reinforced main structure using a limited number of strategically placed, high-capacity connections.
Design Challenges and Solutions
Panel Design and Detailing: McClure designed and detailed the exterior prefabricated CFS panels and 3D volumetric aluminum façade panels through an integrated process:
- Created prefabricated panel details allowing each installation to “drop in” seamlessly to the previous, accelerating installation and reducing field labor.
- Created multistory prefabricated panels, each with connections only to the ‘jamb’ element. The building has stepping panel locations, so this required coordination of the CFS vertical and horizontal movement joints.
- Engineered a standalone CFS mock-up system, including a cantilevered soffit, to validate design assumptions before full-scale implementation. (Figure 1)
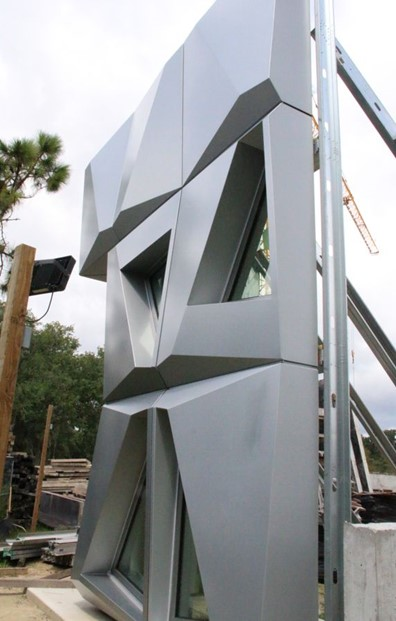
|
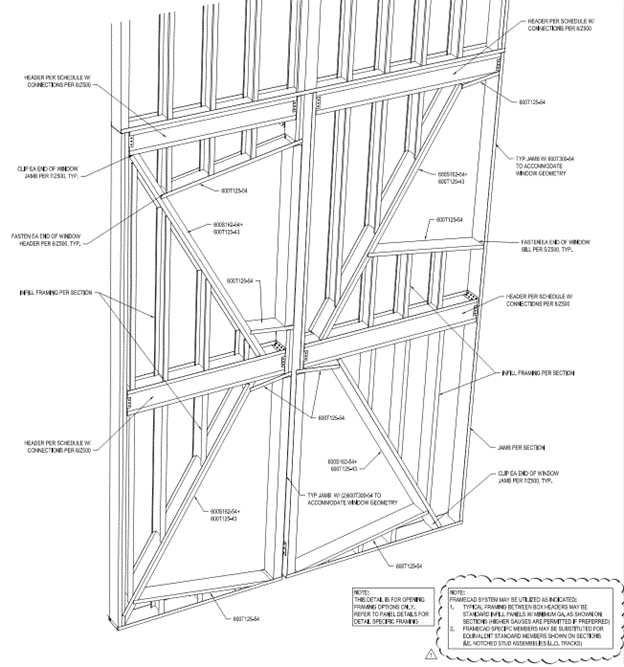
|
- Designed identical jamb and beam system for each panel, with the window module and wall modules swappable to ensure the most efficient and redundant construction system. (Figure 2)
- Created color and symbol-coordinated drawings to convey attachment locations and show how the panels interact with adjacent panels. This descriptive system allowed McClure to easily coordinate 22 uniquely engineered and attached panel layouts during installation. (Figure 3)
- Designed aluminum cladding and its coordinated attachment to the perimeters and opening framing of the CFS panel system. Preinstalled lock-in rails on each panel’s jamb members allowed the aluminum cladding panels to be quickly dropped in for a finished exterior. These concentrated forces on the jambs and window framing required coordination with the CFS to ensure loads were correctly transferred from the cladding to the CFS system. This prevented the typical wall framing from needing to be designed for wind pressures.
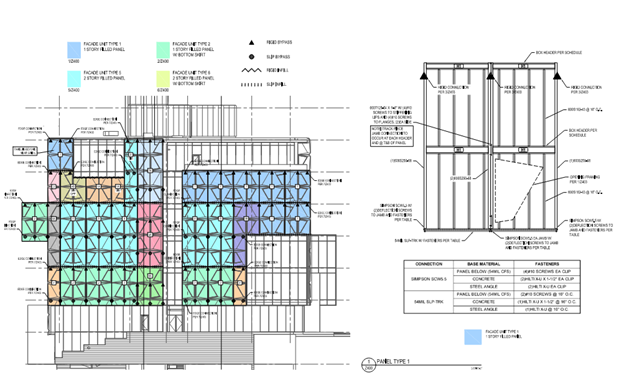
Modular Prefabrication and Installation: The project’s modular approach led to rapid installation, minimal field joints and a watertight enclosure. Key highlights include:
- Large Multi-Story Panels: Designed as multi-story assemblies to limit field joints and expedite construction, each panel’s primary load-carrying jamb members attach to the structure at 8 feet on-center, with horizontal box headers spanning between jambs. (Figure 4)
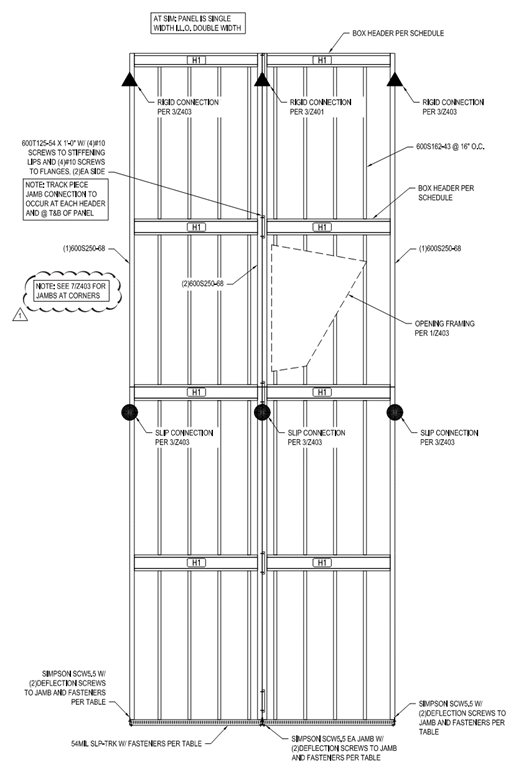
- Highly Adaptable “Wall Module” System: Standardized interior wall modules could be swapped for opening modules where required. The jambs and header framing were kept consistent, so the openings and solid wall sections could be mass-produced and swapped out for repeatability of detailing. (Figure 2)
- Efficient Hoisting & Connection Details: Panels were lifted into place with an engineered hoisting system, using mid-span pick points to safely rotate the panels vertically. Once positioned, each panel was secured using high-capacity Simpson Strong-Tie seismic bypass clips attached to Hilti anchor channels cast in the concrete. With panels having jamb and header systems across all panels (including solid wall segments), attachments to the structure were limited to 8 feet o.c. rapidly speeding up onsite construction. These cast-in-place high-strength connections required BIM coordination to ensure anchors and attachments aligned with premanufactured connections. This setup required only four high-capacity clips per typical multi-story panel, drastically reducing the number of attachments at every panel.
- Prefabricated Aluminum Cladding Coordinated with the CFS System: Preinstalled lock-in rails on each panel’s “jamb” members allowed the aluminum cladding panels to be quickly “dropped in” for a finished exterior. These concentrated forces required coordination with the CFS to ensure loads were correctly transferred from the cladding to the CFS system. This prevented the typical wall framing from needing to be designed for wind pressures.
The University of Florida’s Malachowsky Hall for Data Science and Information Technology exemplifies McClure’s commitment to innovation in cold-formed steel (CFS) design. By incorporating modular prefabrication, standardized components and high-capacity connections, the team delivered an advanced building envelope.
Close coordination across engineering, CFS wall panels, cladding systems and cast-in-place anchors minimized construction issues—only a few panels required post-installed anchors due to misalignment and some trim angle adjustments on corner panels. This project is a testament to fulfilling complex architectural visions through the precision and efficiency of prefabricated construction.
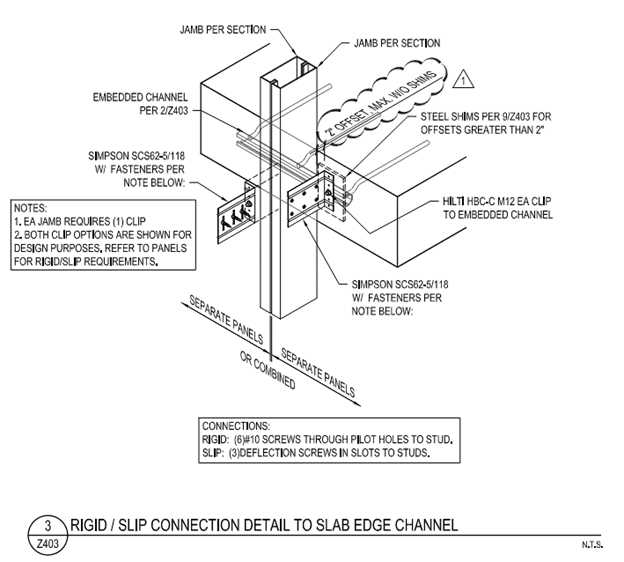
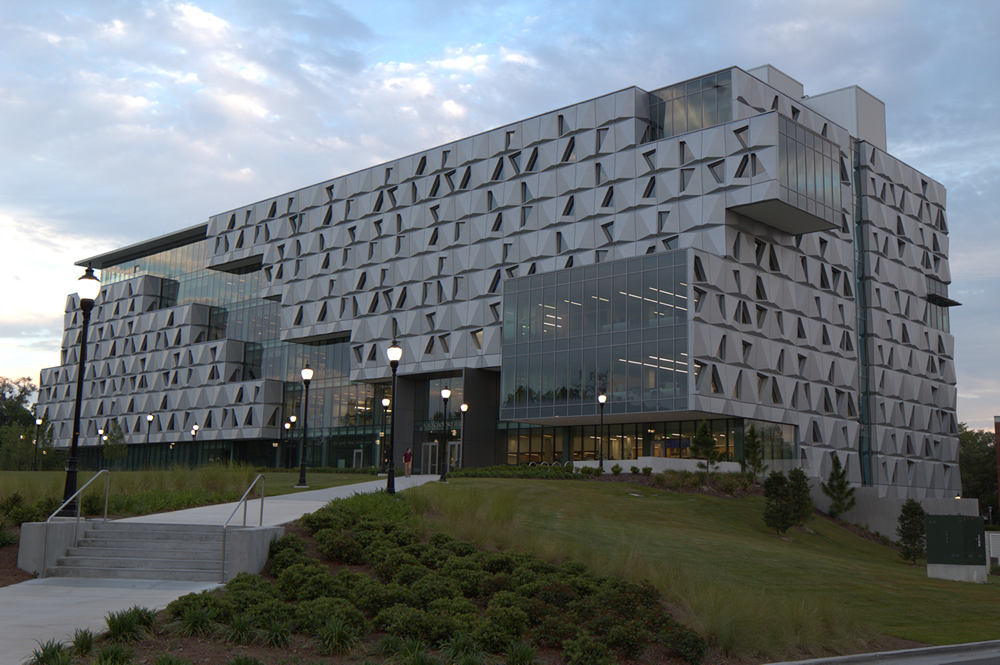
|