2025 CFSEI CREATIVE DETAIL AWARD WINNER
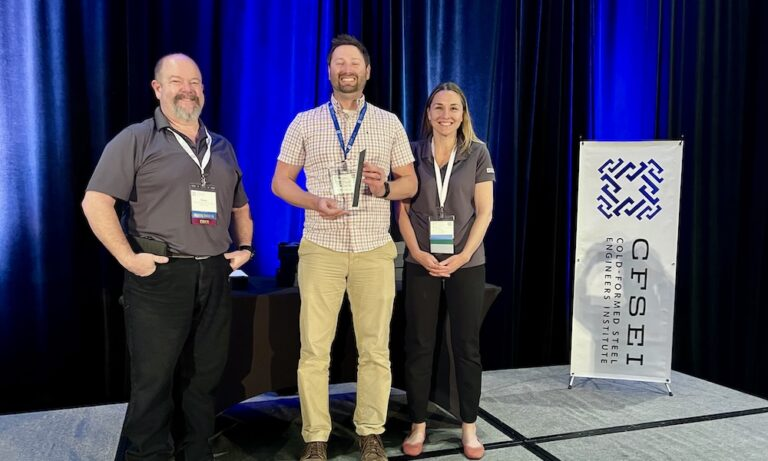
FIRST PLACE
EXCEL ENGINEERING, INC. - HARRAH’S NOLA CIP NEW ORLEANS, LOUISIANA
Harrah’s NOLA CIP 8 Canal Street New Orleans, Louisiana 70130
Completion Date: 2024 Construction Cost: $325 Million
Owner: Ceasars Entertainment Corporation. Architect of Record: CallisonRTKL Professional Corp. (Arcadis). Engineer of Record for Structural Work: Walter P. Moore. Cold-Formed Steel Specialty Engineer:Daniel Church, P.E., Excel Engineering, Inc. Cold-Formed Steel Specialty Contractor: Andy Anderson, King Company LP. Award Entry Submitted by: Daniel Church, P.E., Excel Engineering, Inc.
Project Background
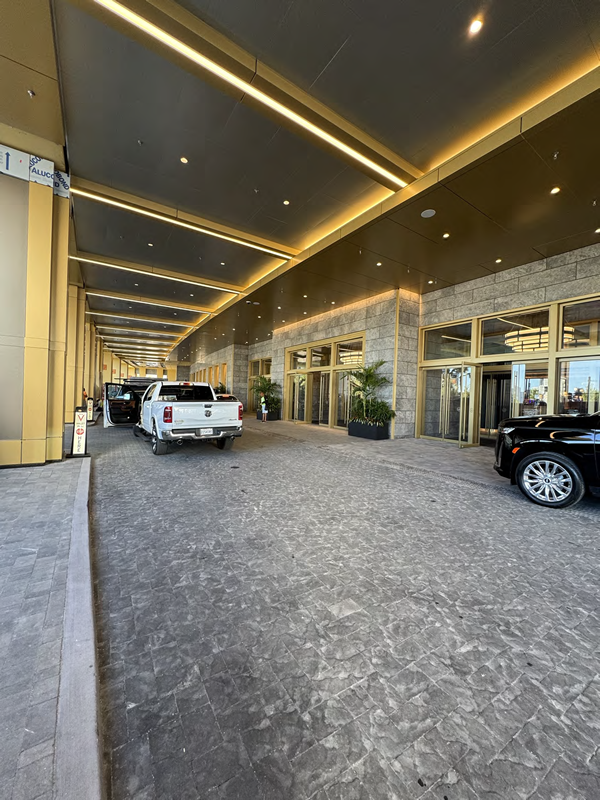
Ceasars Entertainment has completed a new hotel at the Historic Harrah's Casino in New Orleans, Louisiana. Opened in late 2024, the renovation to the existing casino introduced new dining and gaming options. The new 340-room hotel will offer luxurious accommodations. The total cost of the renovations and new hotel tower exceeds $300 million.
Design Challenges and Solutions
When building a 17-story post-tensioned concrete hotel tower in a region such as the Mississippi River Delta, extensive studies need to be done to determine the life-time settlement of the building.
And when this 17-story concrete tower is to be built as an addition to a historic venue in downtown New Orleans, special consideration must be taken so that the two structures will still work together over the lifetime of the structure. (Photo 2)
The owner and design team set a requirement that the first floor of the new hotel match the first floor of the existing casino to make the guest experience between the two buildings seamless. However, floors 2 through 17 had their foundations punched through the matching first floor slabs and had separate footings into the soil below. This created a requirement for differential movement on the first floor. Geological studies set this deflection requirement at between 6"-to-8" of lifetime settlement, which was assumed to take place over a 40-to-50-year period. (Figure 1)
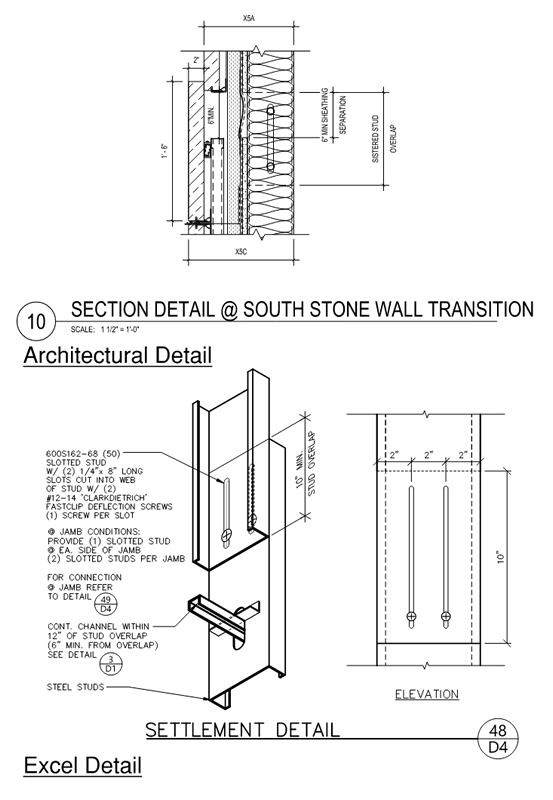
There is extensive cold-formed steel (CFS) framing at the hotel Porte Cochere that would be required to account for that 6"-to-8" of lifetime settlement, a task that cannot be solved with off-the-shelf connectors.
The architectural detail (Figure 2) called for the settlement detail to be in the wall span instead of at the head of the wall using an overlapping detail with a long slot. (Photos 3, 4 and 5)
With no manufactured CFS connectors designed for up to 8" of differential movement, Excel Engineering worked with King Company, a CFS specialty contractor, to come up with a detail to meet the settlement requirements.
It was decided to follow the architectural detail (Figure 1) in principle, but with some revisions to allow for additional stability. An additional slot was added — two total — to prevent it from acting as a hinge during fabrication. The stud was reinforced with a kicker and braced back to post-tensioned level 2 slab. The embedment plates were located so the soffit framing and the wall framing, with required settlement, were attached securely. (Figures 2, 3 and 4)
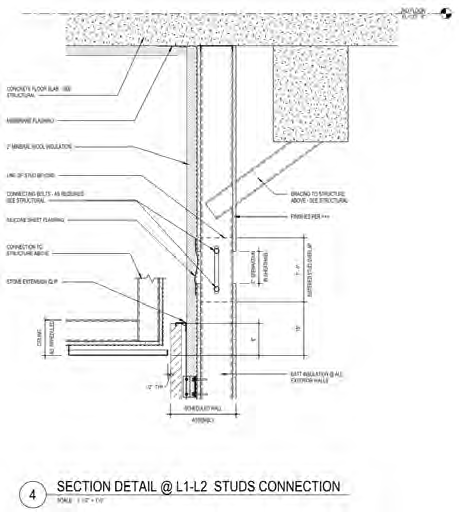
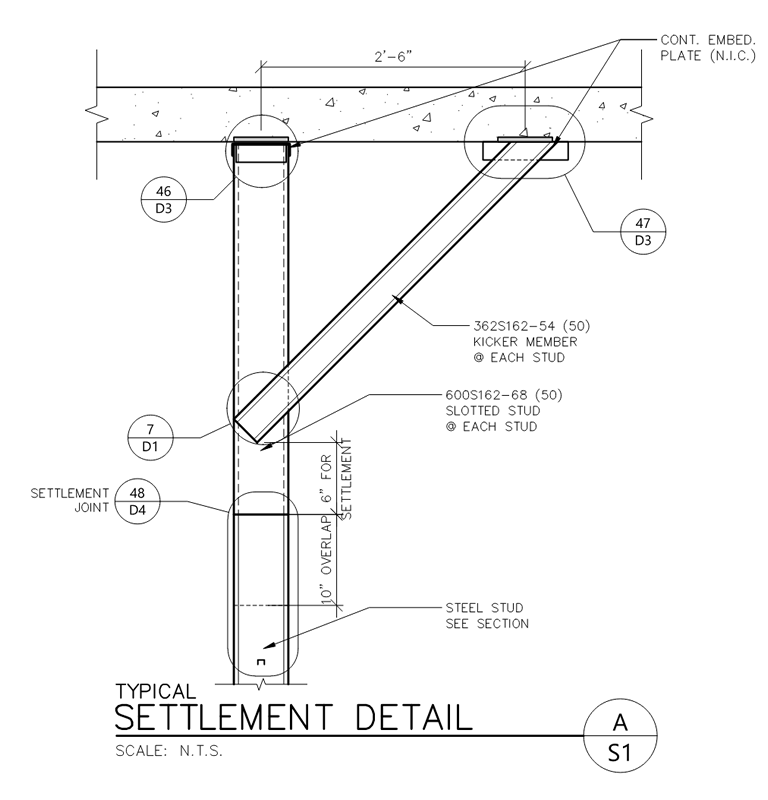
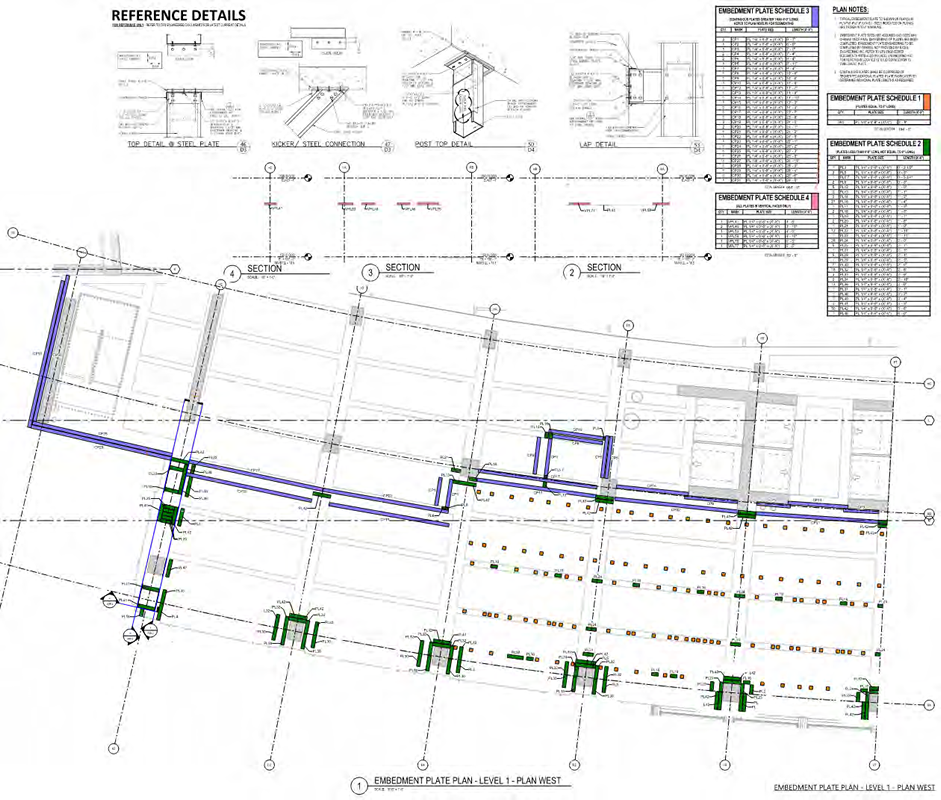
The inclusion of the embedment plates prevented the need for using low-embedment anchors or scanning the slab when attaching the suspended CFS framing.
Excel's in-house BIM coordination team proved invaluable in simplifying the on-site installation and the material take-off. (Photo 6)
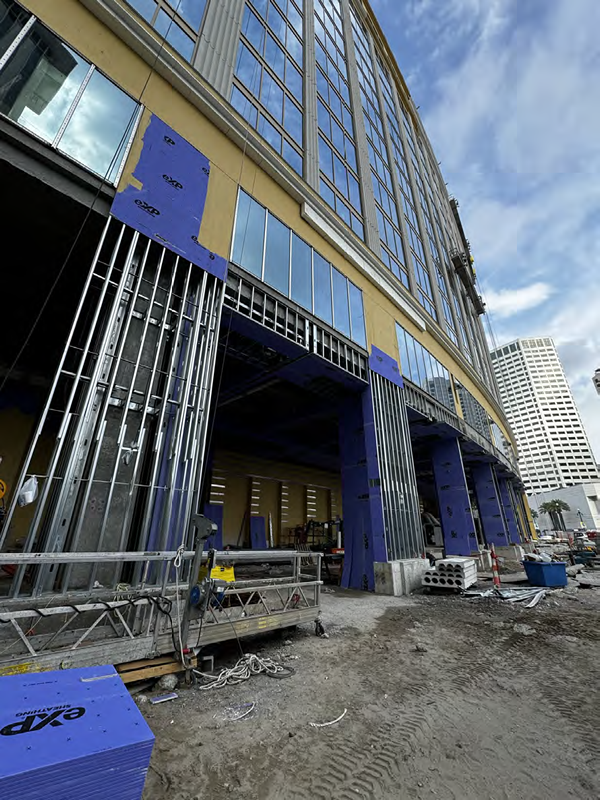
Most of the settlement joints are hidden above the soffit framing to prevent issues with the exterior finishes. The exterior columns, however, were required to have settlement joints at a mid-span location. (Figure 2)
Bracing back to the concrete columns was necessary to properly support and locate the joint at the required location. (Photos 7 and 8)
Execution of such a unique detail required significant coordination between the structural engineer (Walter P. Moore), general contractor (AECOM) and the CFS team (Excel Engineering and King Company).
From fully understanding the requirements of the detail, to the communication to make sure everything ran smoothly, this was a teameffort by everybody involved. (Figure 5)
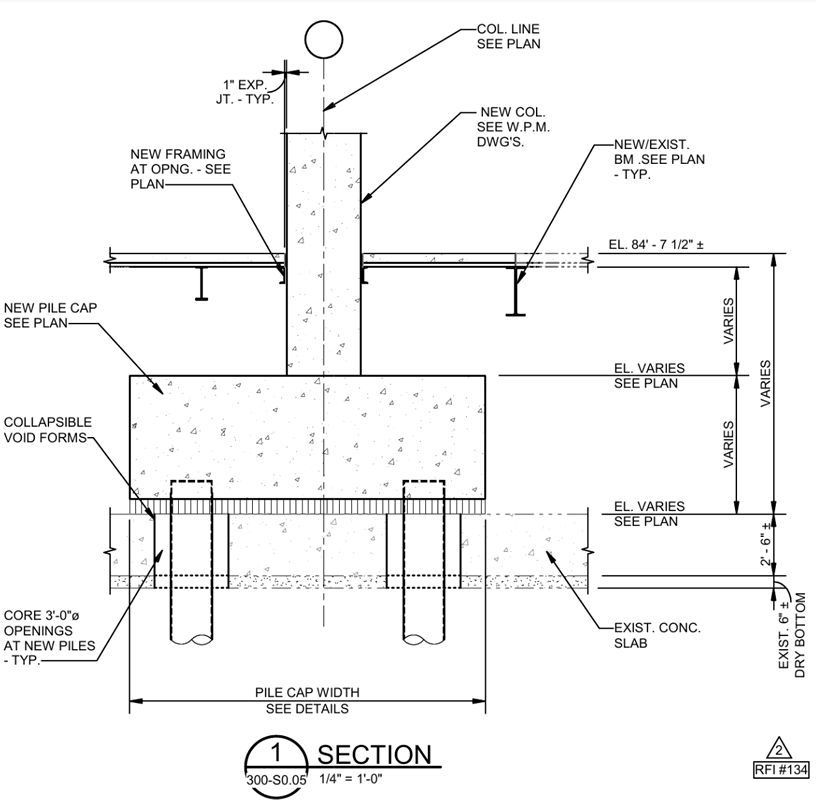
|