2016 CFSEI DESIGN EXCELLENCE AWARD WINNERS
SECOND PLACE
EXCEL ENGINEERING, INC. – THE WHARF 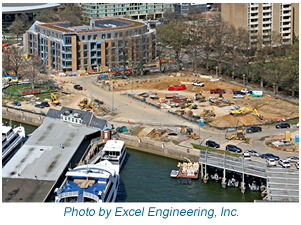
WASHINGTON, DC
The Wharf – 525 Water
525 Water Street, SW
Washington, DC 20024
Completed: December 2015
Construction Cost: $30 million
Owner: RWP, LLC
Architect of Record: SK&I Architectural Design Group, LLC
Engineer of Record for Structural Work: Brian McSweeney, Ehlert Bryan
Cold-Formed Steel Specialty Engineer: Joe Wilkum, Excel Engineering, Inc.
Cold-Formed Steel Specialty Contractor: Trevor Wyman, FrameCo, Inc.
Award Entry Submitted by: Bill Wilde, Excel Engineering, Inc.
Project Summary:
525 Water is a 107-unit condominium building and the first residential project to be constructed in a development known as The Wharf. The Wharf is transforming Washington DC's storied Southwest quadrant by creating a mile-long waterfront neighborhood that includes retail, residential, hospitality, offices, cultural, public park and piers. Featuring views of the Potomac River and fronting a new 3.5-acre Waterfront Park, these new condominiums extend five stories above grade, containing over 105,000 square feet. The building is primarily a square shape, with a curved southern exposure matching the radius of the streetscape. Its courtyard offers landscaped scenery and natural lighting for residents of the interior units. Other amenities include a club room, private rooftop, balconies, green roof, and a two-story garage substructure.
Most of the project consists of load-bearing cold-formed steel framing. The wall panels support concrete over Hambro joists for levels three through the roof. Containing complex curves and angles, the wall framing was prefabricated off-site by FrameCo, Inc., totaling over 9,000 lineal feet. On May 5, 2015, the first of over 1,040 panels was placed on the second floor. In just three months, the structure was topped out with its final pour at the roof. Masonry elevator and stair shafts occur, but the cold-formed X-braces stabilize the building above the second level. The garage and first-level structure are constructed with concrete columns supporting reinforced two-way concrete slabs. The first-story exterior walls are fabricated with cold-formed steel framing containing deflection track at the top of the wall and were installed after much of the second story was already in place.
The exterior facade is composed primarily of brick, metal panels, and glass. Some of the brick required support from the cold-formed walls and openings. A prominent feature of the exterior is the tower occurring at the building’s southwes t corner, which contains floor-to-ceiling glazing supported by miscellaneous cold-formed shapes and structural steel.
The new building rests on the former site of St. Augustine's Episcopal Church. As part of the site, a new church is currently being constructed directly adjacent to the north face of the condominium complex. Some of the 94 newly created parking spaces within the condo project will be shared with the church, establishing a harmonious tie with the community.
Due to an aggressive construction schedule, Excel Engineering, Inc. developed an innovative process to quickly communicate new information among team members. Requests for Information (RFIs) were submitted well before the engineering was completed, and a level of importance was assigned to each request so the design team could address time-sensitive issues first.
Excel also provided a level of accelerated service by handling complicated aspects directly with the project design team. This coordination process alerted the design team of potential issues, allowing them to be resolved before they could create delays. For instance, in-depth coordination with the stair fabricator was required for beam design at the fifth-level stair openings. By anticipating the need and addressing it upfront, Excel was able to quickly produce accurate wall panel elevation drawings.
The impact of cold-formed prefabricated panels on this project is best exemplified by the beam pockets that were required. With over 100 steel beams at the fifth level, Excel coordinated beam depth, width, and bearing location so cold-formed posts could be provided. The posts were capable of supporting each beam, as well as allowing adequate space for the field to make their connections. This avoided costly delays associated with traditional iron work. Adding to the complexity, more than 550 MEP (mechanical, electrical and plumbing services) sleeves penetrated each level. Excel coordinated every stud location to avoid interference and support a much faster installation of the wall panels.
Shear walls are an integral part of many projects. Aligning posts floor-to-floor, especially through concrete, is difficult. Excel worked with FrameCo to solve this challenge with a creative solution. Taller cold-formed shear wall posts with cap plates wer e designed and supplied within each panel. The panel above contained slots in its bottom track at these posts, enabling the field to properly align the shear wall post while directly welding each assembly together. Due to the nature of the project, some shear walls were not able to be shipped full-length. Therefore, Excel created an overlap detail to maintain continuity across the splice between shear wall panels. This involved welding a plate that extended past the end of one panel so it could be fastened to the adjacent panel once set in the field.
Combining attention to every detail with an innovative design, Excel and FrameCo demonstrated that prefabricated cold-formed steel systems work perfectly as the primary structure for any mid-rise building.
Download Case Study 